Vom Reststoff zum Rohstoff
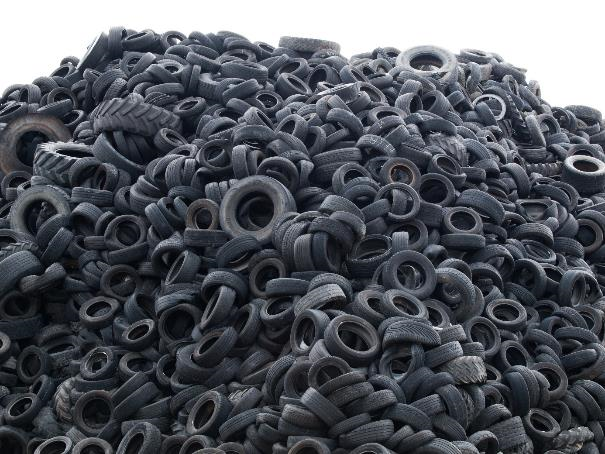
100 Jahre Makromolekulare Chemie
Innovation ist der Treiber für nachhaltiges Wachstum. Dessen Erfolgsrezept hängt allerdings von vielen Variablen ab. Im Zeitalter knapper Ressourcen ist effiziente Kreislaufwirtschaft eine davon. Dabei spielt die chemische Industrie eine Schlüsselrolle. Wie man einen Reststoff wie Altreifengummi effizient zu einem robusten Wertstoff verarbeitet und in den Produktionskreislauf wiedereinführt, ist im folgenden Artikel aufgezeigt.
Kaum ein anderer Industriezweig leistet einen derartigen Beitrag zu mehr Nachhaltigkeit wie die Chemiebranche. Chemieunternehmen beschäftigen sich seit Jahren nicht nur damit, eigene Treibhausgasemissionen, Wasserverbrauch oder Abfallmengen zu reduzieren. Sie haben das Thema „Nachhaltigkeit“ zur Chefsache gemacht und es in die Unternehmensstrategien verankert. Vor allem jedoch machen Spezialchemieprodukte umweltschonende Innovationen erst möglich.
Chemie macht Umweltinnovationen erst möglich
Wie man etwa Stoffkreisläufe mit Chemieprodukten nachhaltig schließen kann, zeigt das Beispiel von VESTENAMER®: Das Kautschukadditiv ermöglicht es, Altreifengummi zu einem robusten Werkstoff effizient zu verarbeiten, aus dem beispielsweise Bodenbeläge, Komfortprodukte für Nutztiere oder Rohstoff für modernen Straßenbau hergestellt werden.
Alles beginnt beim Kautschuk. Davon werden laut dem europäischen Verband der Reifen und Gummihersteller ETRMA weltweit zirka 29 Millionen Tonnen produziert, davon gut die Hälfte als Synthesekautschuk aus fossilen Quellen, und die andere Hälfte als Naturkautschuk, der größtenteils in asiatischen Ländern erzeugt wird. Der Naturkautschuk wird von den verarbeitenden Industrien durch energieintensives Mischen und Formprozesse wie Kalandrieren, Extrudieren oder Pressformung zu einer Vielfalt an Gummiprodukten verarbeitet. Erst durch den Vulkanisationsprozess und die Beimischung von Füllstoffen und funktionalen Additiven bekommt er dann seine gewünschten Eigenschaften.
Der größte Abnehmer für Kautschuk stellt die Reifenindustrie dar. Freedonia erwartet dass der weltweiten Bedarf in den nächsten Jahren auf mehr als 3 Milliarden Reifen pro Jahr wächst, was laut den Marktforschern von IHS Markt etwa 70 % der weltweiten Naturkautschukproduktion in Anspruch nimmt.
Reifen haben kurze Lebensdauer
Aufgrund des mechanischen Abriebs ist die Lebensdauer von Reifen auf wenige Jahre begrenzt. Reifenentwickler stehen bei der Entwicklung immer vor einem Zielkonflikt zwischen den Eigenschaften Abrieb, Rollwiederstand und den Sicherheitsaspekten des Reifens wie Nass- und Trockenhaftung. Laufleistung, und Kraftstoffverbrauch, bzw. die CO2 Emissionen, können daher nicht beliebig unabhängig voneinander verbessert werden, ohne dabei Kompromisse bei der Sicherheit einzugehen.
Das World Business Council for Sustainable Development (WBCSD) schätzt, dass derzeit etwa eine Milliarde Reifen jedes Jahr das Ende ihrer Lebenszeit erreichen. Auf Deutschland entfallen davon etwa 600 000 Einheiten ausgedienter Fahrzeugreifen. Der steigende Mobilitätsbedarf verursacht schlussfolgernd Herausforderungen für die Umwelt:
In Deutschland werden laut dem ETRMA-Report heute nahezu 100 % der Reifen wieder eingesammelt und verwertet. Zertifizierte Altreifenhändler sorgen für Qualitätsstandards und bringen Transparenz in den Markt. Reifen sind daher ein sehr gut zu sammelndes und sortierbares Produkt. Es bleibt allerdings die Frage – wohin mit diesem gewaltigen, sekundären Rohstoffstrom?
Zweites Leben für Autoreifen
Ein durchschnittlicher Reifen hat einen respektablen Energiegehalt von 33 Megajoule pro kg wie vergleichende Lebenszyklusanalysen bescheinigen. Das übertrifft gar den Brennwert von manchem nativen Brennstoff wie z. B. Kohle. Die thermische Verwertung erscheint damit eine naheliegende Entsorgungsoption, was in Deutschland historisch auch der primäre Werdegang des ausgedienten Reifens war, z. B. für die Befeuerung von Zementöfen.
Bei genauerer Betrachtung moderner Reifen wird allerdings offensichtlich, dass diese ein werthaltiger Rohstoff sind, der sich für die stoffliche Verwertung besonders gut eignet. Heutige Reifen sind äußerst komplexe High-tech-Produkte, die aus mehr als einem Dutzend Teilen, Kautschukmischungen und verstärkenden Elementen aufgebaut sind. Da Polymer und Ruß nach der Vulkanisation fest miteinander verbunden sind, entspricht der nutzbare Elastomeranteil des verwerteten Reifens etwa 70 %.
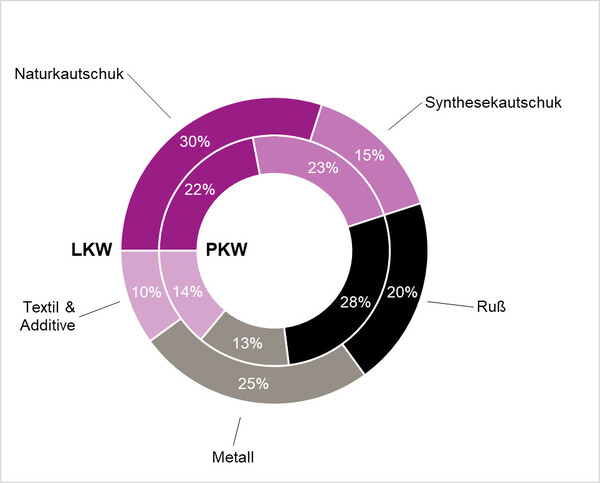
Durchschnittliche Zusammensetzung von Fahrzeugreifen (Quelle: Sienkiewicz et al. Water Management 32 (2012), 1742-1751).
Vor 20 Jahren wurde allein in Deutschland noch mehr als die Hälfte der anfallenden Altreifen der energetischen Verwertung zugeführt, während nur etwa jeder zehnte Altreifen für die stoffliche Verwertung zu Granulat verarbeitet wurde, um erneut in den Kreislauf eingeführt zu werden. Letztere liegt mittlerweile mit der energetischen Verwertung auf Augenhöhe. Ein aus ökologischer Sicht sinnvoller Verwertungspfad, wie die gemeinsame Studie des Instituts für Energie- und Umweltforschung Heidelberg ermittelt hat: Jedem Kilogramm stofflich verwertetem Reifenmehl oder Granulat können 2,6 kg Kohlenstoffdioxid Emissionsersparnis gegenüber der thermischen Verwertung gutgeschrieben werden.
Einen modernen und kosteneffizienten Ansatz für die Zweitverwendung von Reifen verfolgt Evonik. Der Zusatz von VESTENAMER®, einem Prozessadditiv für die Gummiindustrie, ermöglicht Gummimehl aus Altreifen zu einem gummihaltigen Asphalt zu verarbeiten. Der wiedergewonnene Werkstoff wird Straßenbaubitumen oder Straßenbauasphalten beigemischt, um die Qualität zu verbessern und die Dauerhaftigkeit von Straßenbelägen zu verlängern.
Das Trans-Polyoctenamer (TOR) ist chemisch betrachtet selbst ein echter Spezialkautschuk und vernetzt auch als solcher. Es hat allerdings im Gegensatz zu klassischen Kautschuktypen thermoplastische Eigenschaften und einen niedrigen Schmelzpunkt, weshalb es bei moderaten Temperaturen aufgeschmolzen und zur Beschichtung des Gummimehls verwendet werden kann. Diese trickreiche Wirkweise macht das Recyclingmaterial wieder verarbeit- und vernetzbar.
Die Verwendung von Gummimehlen in Asphaltanwendungen wurde in den 1950er Jahren in den USA entwickelt. Man ging damals davon aus, dass die Rissbildung als wesentlicher Grund für den Verfall von Asphaltdeckschichten deutlich reduziert werden kann. Inzwischen wird in der globalen Straßenbau-Industrie der positive Beitrag von Gummimehlen zur Vermeidung von Rissbildungen, aber auch der Standfestigkeit, also dem Widerstand gegen plastische Verformung, die sich wiederum in der Spurbildung im Straßenbelag ausdrückt, anerkannt.
Wie lange hält eine Straße?
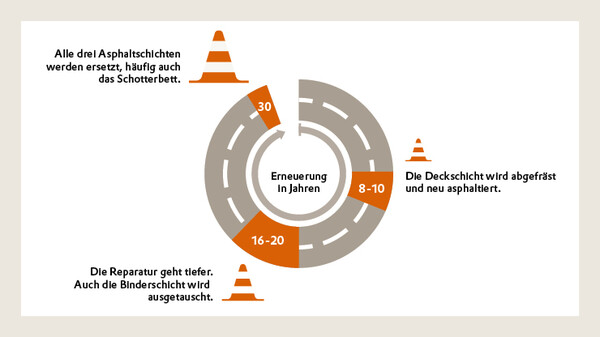
Bildunterschrift: Straßen werden in der Regel für eine Lebensdauer von 30 Jahren angelegt. Einzelne Schichten müssen je nach Belastung früher erneuert werden. (© Evonik)
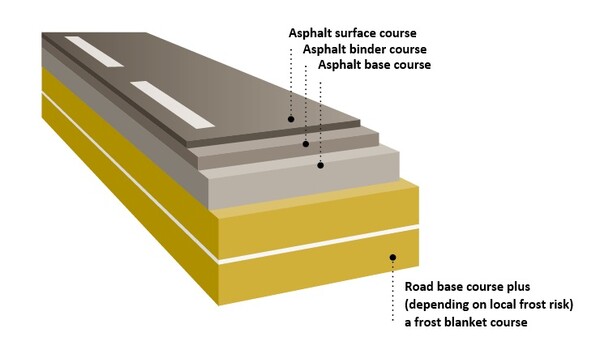
Bildunterschrift: Autobahnen bestehen aus vier Lagen. In drei davon kommen Asphalt und Altreifen zum Einsatz. (© Evonik)
Neben den klimatischen Einflüssen stellt der zunehmende Schwerlastverkehr den Straßenbau vor Herausforderungen. Im Transitland Deutschland werden jährlich über 40 Mio. Tonnen Asphalte hergestellt. Der Anteil modifizierter Asphalte liegt mit zirka 30 %, überdurchschnittlich hoch. Die Verwendung von Gummimehlen spielte dabei bis vor wenigen Jahren kaum eine Rolle, da zunächst wesentliche Punkte bei der Herstellung und der Verarbeitung von Gummimehlen in Asphaltbauweisen Beachtung finden müssen. Dass die bautechnische Umsetzung mittlerweile ohne Kompromisse bei der Verarbeitung möglich ist, wurde erst kürzlich wieder in einem deutschen Pilotprojekt mit VESTENAMER® demonstriert.
Mehr Effizienz bei Gummirecycling
Ökologisch sinnvoll ist die Nutzung von Altreifen allemal. Mit der Wiederverwendung gebrauchter Autoreifen werden wertvolle Ressourcen gesichert. Gummimehle aus Reifen am Ende ihres ersten Lebenszyklus können weitere zehn bis zwölf Jahre durch die Verwendung in Asphaltdeckschichten im Kreislauf gehalten werden. Diese übertreffen in der Regel die Haltbarkeiten unmodifizierter Asphaltdecken, welche üblicherweise nach acht bis zehn Jahren ausgetauscht werden müssen (siehe Bild).
Das Reifenrecycling sowie die sinnvolle Verwertung des wiedergewonnene Rohstoffes Reifenmehl ist heute aktueller denn je. Die europäischen Bestrebungen in Richtung Kreislaufwirtschaft und der anhaltende Trend zur stofflichen Verwertung prognostizieren eine aussichtsreiche Perspektive für Innovationen in diesem Bereich.
Autoren: Dr. Alexander Paasche, Frank Lindner, Dr. Peter Hannen, Janusz Berger,
Evonik Resource Efficiency GmbH, Marl
Redaktionelle Bearbeitung: Maren Mielck, GDCh
Quellen:
[ETRMA] ETRMA, “European Tyre & Rubber Industry – Statistics”, 2019.
[Freedonia], Freedonia, “Global Tires”, Industry study #3687, 2018.
[IHS] IHS Markit, „Rubber, Natural“, Chemical Economics Handbook, 2018.
[WBSCD] World Business Council for Sustainable Development, “Global ELT Management – A Global State of Knowledge on Collection Rates, Recovery Routes, and Management Methods.”, 2018.
[LCA] Feraldi, Rebe, Sarah Cashman, Melissa Huff, and Lars Raahauge. “Comparative LCA of Treatment Options for US Scrap Tires: Material Recycling and Tire-Derived Fuel Combustion.” The International Journal of Life Cycle Assessment 18, no. 3 (2013): 6
[EU Review] Sienkiewicz, Maciej, Justyna Kucinska-Lipka, Helena Janik, and Adolf Balas. “Progress in Used Tyres Management in the European Union: A Review.” Waste Management 32, 10 (2012): 1742–51.
[IFEU] Bakas, Ioannis, Birgitte Jørgensen Kjær, Anders Schmidt, Nanja Hedal Kløverpris, Regine Vogt, and Jürgen Giegrich. “Ökobilanzieller Vergleich Zweier Verwertungsalternativen Für Altreifen: Stoffliche Verwertung Und Mitverbrennung Im Zementof
[IEC] Paasche, Alexander, Frank Lindner, Peter Hannen, Marco Gensheimer, and Ankur Kant. “Pushing Boundaries! - VESTENAMER® in Recycling Rubber Applications.” In International Elastomer Conference 2019, 196th Technical Meeting - Fall 2019, Rubber Div
[PTM] Gogolin, Daniel. “Die Performance stimmt.” Asphalt & Bitumen, 06 (2019): 30–35.
Kommentare
Keine Kommentare gefunden!