Polymere im Schuh
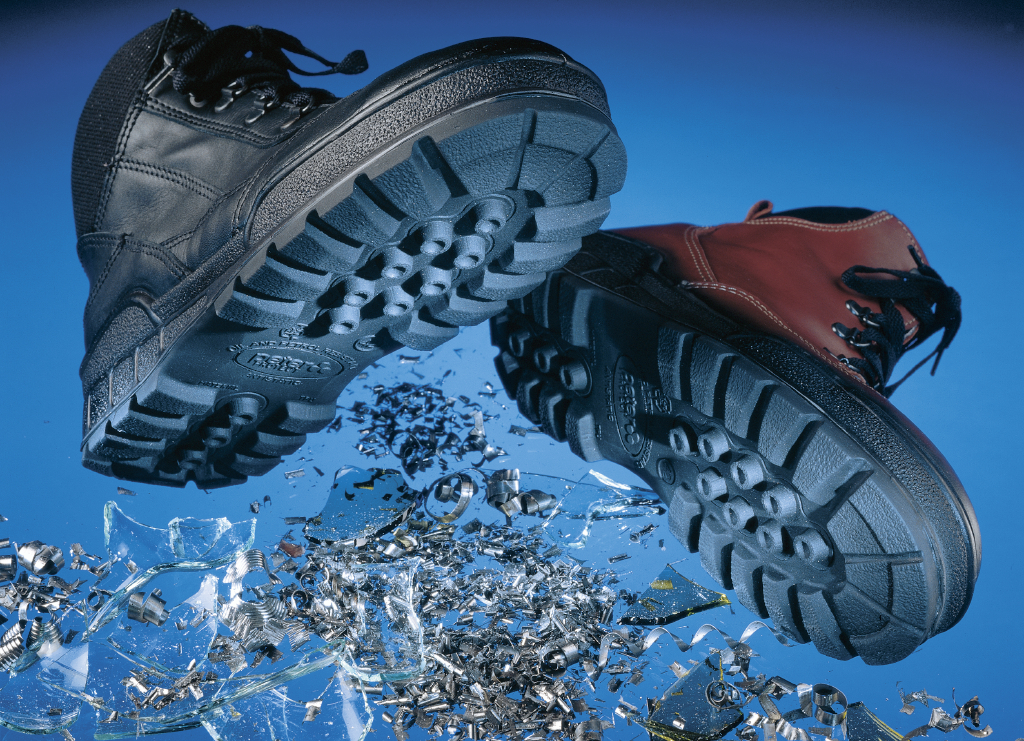
100 Jahre Makromolekulare Chemie
Schuster bleib bei deinen Leisten.“ So heißt das alte Sprichwort, mit Hilfe dessen man nicht zu weit über seine Talente hinaus agieren sollte. So war es über Jahrhunderte üblich, aus einem Leder den Schuhschaft über dem Leisten anzufertigen, der dann mit einer Ledersohle mit Hilfe von Nägeln zu einem fertigen Schuh verbunden wurde. Eleganter war das Vernähen der Sohle mit dem Schuhoberteil oder das Verkleben, als geeignete Materialien verfügbar waren. Je nach Machart wendet man heute noch alle diese Verfahren an. Die Revolution begann im 20. Jahrhundert mit dem Einzug der Kunststoffe in diese Branche. Der Naturwissenschaftler spricht bei den Kunststoffen von Makromolekülen oder Polymeren, weil ein „Plastik-Werkstoff“ aus großen Molekülketten besteht. Je nach chemischer Struktur wird dem Namen des Werkstoffes ein „Poly“ vorangestellt. So findet man bei einem modernen Schuh, der nicht aus Leder oder Naturfasern besteht, Materialien wie Polyurethane, Polyethylen-vinyl-acetate, Polyester, Polyamide und zu geringerem Teil noch andere.
Doch warum macht man das? Die Polymere bieten mehr Möglichkeiten, einen Schuh leichter zu machen, den Tragkomfort zu verbessern oder verschiedene Designs zu realisieren. Mittlerweile werden über 20 Milliarden Schuhpaare weltweit produziert und verkauft, über 50% davon bestehen aus Kunststoff und Gummi. Gummi, wohlgemerkt, ist ebenso ein Polymer. Andere große Mengen sind nach wie vor Leder oder Textil, die im Schuh Anwendung finden.
In den folgenden Abschnitten betrachten wir die wesentlichen Teile am Schuh – die Schuhsohle, die dämpfende Zwischenschicht und den Schuhschaft.
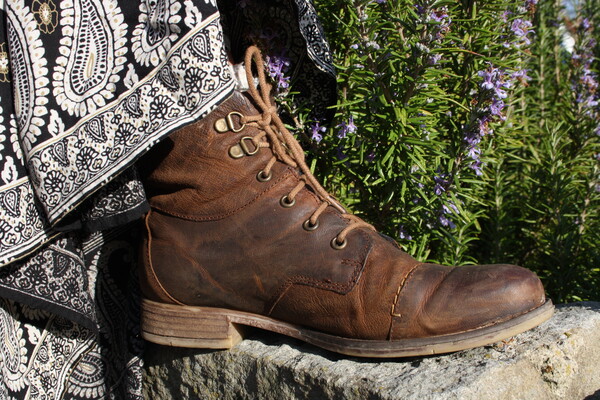
Abb. 1: Damen-Lederschuh, © G. Scholz
Die Schuhsohle
Eine moderne Schuhsohle besteht aus einer Außen-, einer Zwischen- und meist noch einer Innensohle, die auch Brandsohle genannt wird. Alle diese Sohlen haben ganz unterschiedliche Aufgaben, sodass jeweils geeignete Werkstoffe eingesetzt werden.
Die Außensohle soll gewährleisten, dass der Träger einen guten Halt auf dem Untergrund beim Gehen und Laufen hat. Der Wanderschuh (Abb. 2) besteht aus einer robusten Platte mit einem ausgeprägten Profil für ein gutes Gehen in unwirtlichem Gelände. Der elegante Büroschuh hat meist eine flache Ausprägung. Daher findet immer noch der Lederschuh einen guten Absatz.
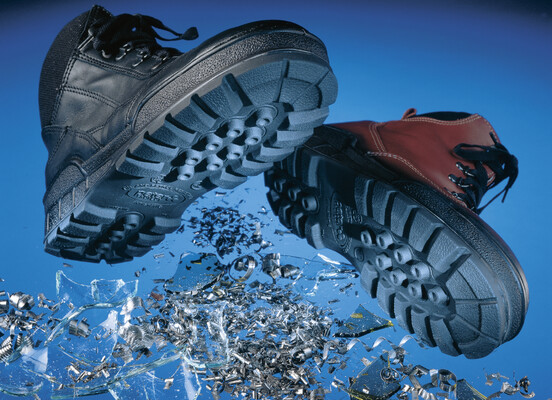
Abb. 2: Wander- oder Treckingschuh. ©BASF
Der größte Teil wird jedoch der Gummisohle zugeschrieben, sowohl für den Straßen- als auch für den Laufschuh. Nicht nur dass die Profilgestaltung gern von den Reifentechnologen abgeguckt wird, auch die Gummirezeptur entspricht häufig einem Material für Autoreifen, also einem SBR (Styrene-Butadiene-Rubber) oder NR (Natural Rubber). Nur mit Ausnahme des Naturkautschuks (NR) sind es immer synthetische Polymere, aus denen Gummi hergestellt wird. Damit das Material brauchbar wird, muss eine Mischung mit Füllstoffen, meist Ruß, und Vernetzern erstellt werden. Presst man die Mischung zu einer Sohle, muss sie vulkanisiert werden, das heißt beim Erhitzen vernetzen die großen Moleküle zu einer festen Masse. Einfacher ist es bei dem häufig verwendeten Polyurethan-Granulat, das in einer Maschine aufgeschmolzen und unter hohem Druck in eine Sohlenform gepresst wird. Beim Auskühlen verfestigt es dann. Man spricht auf stofflicher Ebene von einem physikalischen Netzwerk im Gegensatz zum chemischen Netzwerk beim Gummi. Den beschriebenen Verarbeitungsprozess nennt man Spritzguss. Am Ende entscheiden die Ansprüche der Kunden, welche Sohle geeignet ist – also Eigenschaften der Trittsicherheit, Rutschfestigkeit auf nassem Boden bis hin zu Laufgeräuschen. Diese beeinflusst der Polymerstoff, aber besonders auch die Gestaltung des Profils. Nicht zu vergessen ist neben der Funktionalität das Aussehen des Schuhs. Selbst die Schuhsohle wird häufig zum Designelement (Abb.3). In der Herstellung wird die Grundplatte immer wieder mit verschieden eingefärbten Kunststoffen im Spritzgussprozess aufgebaut, um den aufwändigen Klebeprozess zu umgehen.
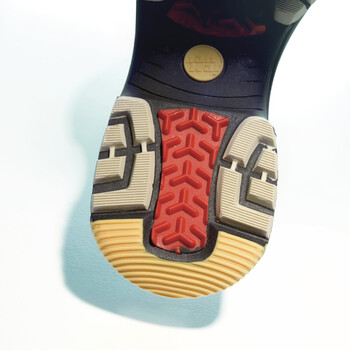
Abb. 3: Straßenschuh. ©BASF
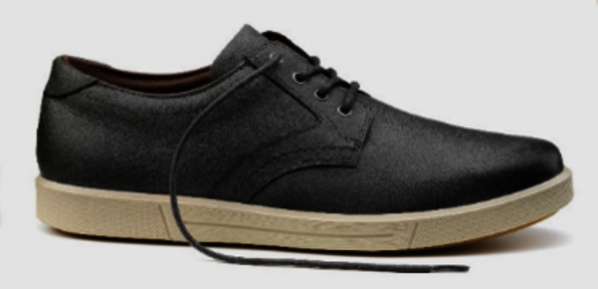
Abb. 4: Freizeitschuh oder Sneaker. ©BASF
Wichtig für das angenehme Auftreten ist die Zwischensohle – nicht nur beim Laufschuh. Anthropologisch gesehen, ist das barfüßige Gehen am gesündesten für den Menschen, dennoch bevorzugen wir die Wärme und Dämpfung des Schuhs. Beides wird erreicht durch eine Schaumschicht zwischen Fuß und Außensohle. Dieser Schaum muss elastisch sein, darf in der Kälte nicht spröde werden und soll seine Struktur möglichst lange bewahren. Es gibt verschiedene Technologien, die den an den Schuh bringen. Häufig wird ein leicht fließender Werkstoff mit Treibmittel in eine Form gebracht und durch Temperatur ausgehärtet. Meist dient dazu Polyethylen-vinyl-acetat (EVA). Das fertige Teil verklebt man mit der Außensohle und dem Oberteil. Dieses Verfahren ist weit verbreitet bei Lauf- und Freizeitschuhen, weil dieser Schaum sehr leicht ist und eine ausreichende Lebensdauer hat. Im Fall von Polyurethan, dem anderen häufig verwendeten Kunststoff im Schuh, werden zwei Komponenten mit Treibmittel in eine Form gespritzt, in der die Reaktion zum Polymer unter Bildung einer Schaumstruktur abläuft. Da Polyurethan gut kleben kann, wird das Gemisch teilweise direkt zwischen Sohle und Schaft eingebracht (hellblaue Schicht in Abb. 5), sodass ein anschließendes Verkleben nicht mehr notwendig ist. Das klingt einfach, doch ist der maschinelle Aufwand deutlich höher.
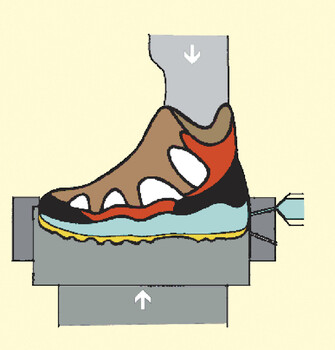
Abb. 5: Direktansohlung. ©BASF
Neben einigen exotischen Konstruktionen haben sich der Partikelschaum und das Luftpolster etabliert. So kann ein Granulat bereits in geschäumter Form hergestellt werden, wie man es vom Styropor kennt, nur dass dieser Partikelschaum elastisch ist. Die Kügelchen werden in einer Form zusammengepresst und mit heißem Wasserdampf miteinander verschweißt. Ebenso können sie verklebt werden – oft bei kleinen Stückzahlen der Fall. Aufgrund seiner Beschaffenheit hat eine Zwischensohle aus Partikelschaum immer eine höhere Rückstellkraft als ein oben beschriebener Schaum, obwohl die Dichte, also das spezifische Gewicht, auf gleichem Niveau liegt. Nur ein Schaum aus EVA ist noch leichter, wenn auch weniger haltbar.
Was aber ist ein Luftpolster am Schuh? Wenn man eine Folie aus elastischem Kunststoff zu einer Blase verschweißt und Luft einbläst, entsteht ein Luftpolster – wie bei einem Luftballon. Die Folie wird in der sogenannten Extrusion hergestellt, bei der Granulat auf einer drehenden Schnecke im Zylinder aufgeschmolzen und durch eine flache Düse ausgetragen wird, wo das Material auskühlt und als Folie verfestigt. Meist wird das für die Anwendungen am Schuh aus Polyurethan gemacht, wobei der Folienaufbau aus mehreren Schichten besteht, damit die Folie luftdicht ist. Durch spezielle Konstruktionen in der Blase wird die Zwischensohle flach gehalten, schließlich lässt es sich auf einem Ballon schlecht laufen (Abb. 6). Auch solch ein System dämpft gut, ist elastisch und erzeugt ein angenehmes Laufgefühl. In einigen Sportarten jedoch wird die dämpfende Schicht ausgelassen, wie z.B. beim Fußball, Golf, Radfahren.
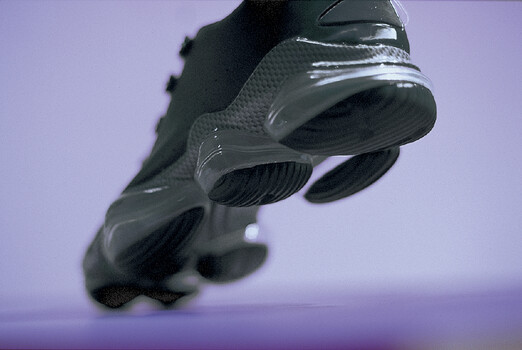
Abb. 6: Laufschuh Nike Air. ©BASF
Der Schuhschaft
Wir haben bereits erwähnt, dass der damals übliche feste Schuh aus Leder bestand und noch heute weit verbreitet ist. Aus einem Lederfell wird ein Teil so herausgeschnitten oder gestanzt, dass das Oberteil über dem Schaft geformt werden kann. Das geht auch mit Polymeren und nicht nur in Form von Kunstleder. Gewebe, die neben natürlichen Textilfasern aus Polyester oder Polyamid hergestellt werden, finden sich mittlerweile in vielen Schuhen. Beispiele sind die beliebten Sneaker oder auch viele Laufschuhe. Abbildung 7 zeigt einen modernen Schuh aus einem gewebten Oberteil und einer Zwischensohle aus elastischem Partikelschaum. Inzwischen laufen bei großen Sportschuhherstellern Projekte, alle Schuhteile aus einem schmelzbaren elastischen Material zu fertigen, sodass der gesamte Schuh nach Gebrauch geschreddert und in einem Aufschmelzprozess im Sinne der Kreislaufwirtschaft sortenrein wieder zu einem verwendbaren Kunststoff im Schuh eingesetzt werden kann.
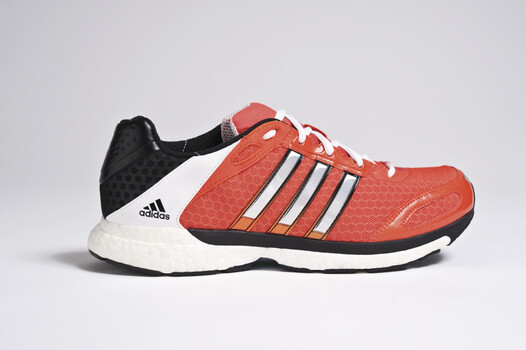
Abb. 7: Laufschuh Adidas. ©BASF
Nicht zu vergessen sind die vielen Designteile an einem Schuhoberteil. Embleme oder Beschriftungen können per Laser, Farbdrucker oder als bedruckte Folie appliziert werden. Letzteres wird in der Regel für Firmenkennzeichen verwendet, da es nicht für jeden Schuh extra angepasst werden muss. Solch eine Folie wird auf Bandanlagen bedruckt und vorgestanzt, sodass die Teile vor Ort von einem Trägermaterial abgezogen, dann aufgeklebt oder aufgebügelt werden. Selbst Sonderteile wie Kappen für Sicherheitsschuhe werden bereits aus Kunststoffen hergestellt damit der Schuh leichter wird.
„Schuster bleib bei deinen Leisten“ heißt natürlich nicht, dass die Entwicklungen von neuen Materialien keine Zukunft haben. In der Welt der Polymere wird es noch viele Neuerungen geben, da ein großes Molekül aus kleinen Bausteinen zusammengesetzt wird und die Auswahl derer noch lange nicht ausgeschöpft ist. Seien wir gespannt, wie sich die Welt der Schuhe weiterentwickeln wird.
Autor: Dr. Günter Scholz (BASF Polyurethanes GmbH)
Redaktionelle Bearbeitung: Lisa Süssmuth, GDCh
Kommentare
Keine Kommentare gefunden!