Mit Polymerfasern zu sauberer Luft
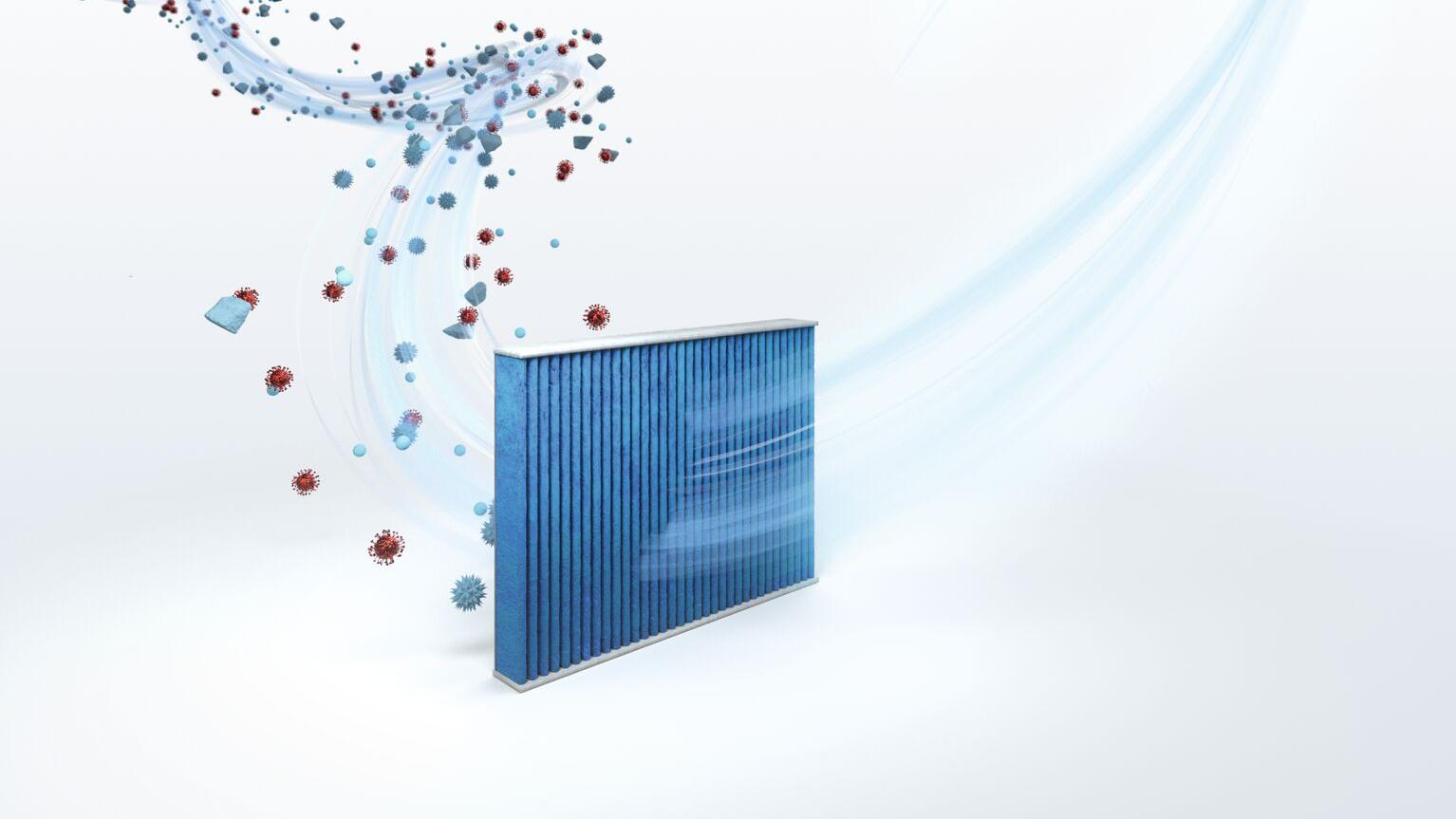
100 Jahre Makromolekulare Chemie
Saubere Luft: Ein Thema, das Filterentwickler mit zunehmender Industrialisierung immer mehr beschäftigt. Gereinigte Luft schützt technische Anwendungen und Menschen gleichermaßen. Vliesstoffe aus Polymerfasern ebneten den Weg für einen Innovationsschub.
Vom Granulat zur Faser…
Schon um 1900 war die Idee geboren, den Motor im Auto durch Filter zu schützen. Papierfilter kamen zum Einsatz und reinigten die Motorzuluft, Öl und Kraftstoff. Einen Schub in der Filtertechnik erlaubte in den 1950er Jahren schließlich die Entwicklung von Filtermedien aus Vliesstoffen auf Polymerbasis. Für Stapelfaservliesstoffe werden vorab gesponnene Polymerfasern in verschiedenen Längen und Feinheiten in Krempelanlagen zu einem Vliesstoff veredelt. Bei Spinnvliesstoffen dagegen werden direkt aus einer Kunststoffschmelze Endlosfasern mit Durchmessern von < 1 bis circa 30 µm zu einem Vliesstoff gesponnen. Die Filamente bestanden in dieser Zeit meist aus Polyester, später kamen Polypropylen, Polyethylen und auch Polyamid als Werkstoffe hinzu. Nach Austritt aus den Spinndüsen werden sie mit Luft gekühlt, verstreckt und danach auf einem Auffangband abgelegt. Die Parameter des Spinnprozesses bestimmen Fasereigenschaften wie Durchmesser, Festigkeit, Dehnung oder Schrumpfung.
… zum Vlies zum Filter
Abhängig von den verwendeten Faserdurchmessern, der Orientierung der Fasern, der Anzahl der übereinander geschichteten Lagen, der Auswahl des Werkstoffs und der Beschichtung ist es heute möglich, individuelle Filtermedien für unterschiedliche Zwecke zu gestalten. Um das lockere Faservlies in einen stabilen Vliesstoff zu verwandeln, stehen verschiedene Optionen zur Verfügung: Der Einsatz von Bindemittel, das nach seiner Aushärtung die Fasern miteinander verbindet. Die thermische Verfestigung, bei der rohstoffgleiche Fasern ohne ein zusätzliches Bindemittel durch zeitweiliges Einwirken einer erhöhten Temperatur erweichen und sich die benachbarten Fasern an den Berührungspunkten verbinden. Oft ist die Polymerfaser dabei auf Kern-Mantel-Basis gesponnen: Der Kern der Faser hat einen etwas höheren Schmelzpunkt als ihr Mantel, sodass dieser während der thermischen Verfestigung aufschmilzt und für die Faserbindung sorgt. Darüber hinaus steht die mechanische Verfestigung zur Verfügung: beispielsweise durch mit Widerhaken versehene Nadeln, die beim Einstechen Faserbündel mitreißen und miteinander verschlingen, so dass sich das Material verfestigt.
Bewährungsprobe in der Industrie
Die ersten Industriefilter bestanden aus einfachen Matten, hergestellt aus Polymerfasern, verfestigt mit Bindemitteln. Sie filtern groben Schmutz und Staub aus der Luft und kommen noch heute beispielsweise als Deckenfilter in Lackieranlagen und als Grobstaub-Vorfilter in mehrstufigen Filteranlagen zum Einsatz. Feine Partikel und größere Schmutzmengen bewältigen die Matten jedoch nicht. Ein Filter, der mehr Staub sammeln kann und auch feineren Staub zurückhält, war gefragt. Ab den 1960 Jahren ließen sich die Entwickler einiges einfallen. Die Geometrie ging weg von der einfachen Matte hin zu Taschen und plissierten Formen wie beispielsweise Kassetten und Patronen. Der Vorteil: Die Oberfläche ist gewachsen, die Filter können mehr Partikel einspeichern, bevor der Druckverlust so groß wird, dass sie ausgetauscht werden müssen. Heute finden sich in industriellen Zuluftanlagen wie Lackierstraßen, bei Gasturbinen oder Klimaanlagen ganze Filterhäuser, in denen unterschiedliche Filter hintereinandergeschaltet sind. Sie schützen frisch lackierte Karosserien vor hässlichen Staubkörnchen, halten flüchtige Kohlenwasserstoffe zurück oder bewahren Gasturbinen vor frühzeitigem Verschleiß.
Der Mensch im Mittelpunkt
Ende der 1980er Jahre rückte eine neue Anwendung in den Blickpunkt der Automobilindustrie: der Kfz-Innenraumfilter. Die ersten Produkte sollten vor allem Pollen und Staub mit Partikelgrößen von größer 3 µm von den Passagieren in der Fahrzeugkabine fernhalten. Der Bauraum für die Filter war begrenzt, große Oberflächen für die effiziente Reinigung dennoch nötig. Die Lösung waren 1 bis 2 mm dicke Spinnvliese, plissiert, um ihre Oberfläche zu vergrößern. Heute leistet ein Kfz-Innenraumfilter weit mehr. Schwebstoffe, Feinststaub, Gase und damit auch Gerüche bleiben im Filter hängen.
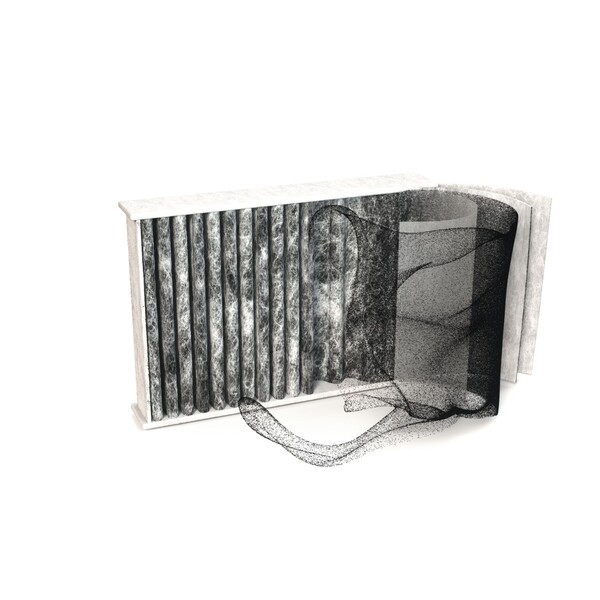
micronAir® Kombifilter schützen vor Feinstaub, Pollen und Ruß und adsorbieren mittels einer Aktivkohleschicht zusätzlich Schadgase und unangenehme Gerüche.
Bildquelle: Freudenberg Filtration Technologies
Darüber hinaus werden durch funktionalisierte Vliesstoffe und Zusatzkomponenten auch anti-allergene und anti-virale Produkteigenschaften realisiert. Mit den gestiegenen Anforderungen hat sich auch das Filtervlies weiterentwickelt. Sehr feine, schmelzgesponnene Fasern aus Polypropylen mit Durchmessern von 0,2 bis 3 µm und im Herstellungsprozess erzeugte elektrostatische Aufladung erlauben es, auch feinste Partikel zurückzuhalten. Der Aufbau moderner Kfz-Innenraumfilter ist komplex und meist eine mehrlagige Kombination verschiedener Vliestypen mit verschiedenen Faserdurchmessern. Von dickeren Fasern am Lufteintritt bis zu den feinsten Fasern am Filterausgang. Der progressive Faseraufbau und die Werkstoffkombination aus Polypropylen und Polyestern ermöglicht es, feine Fasern aus Polypropylen mit den steiferen, aber auch dickeren Polyester-/oder Polypropylenfasern zu einem eigenstabilen plissierbaren Vliesstoff zu formen, der in Kombination mit einer speziellen Vliesstoffschicht mit eingebundener Aktivkohle auch Gase und Gerüche eliminiert. Der Vorteil für die Passagiere in der Fahrgastzelle liegt auf der Hand: saubere Luft ohne lungengängige Feinststäube, ohne Pollen und ohne toxische Gaskomponenten.
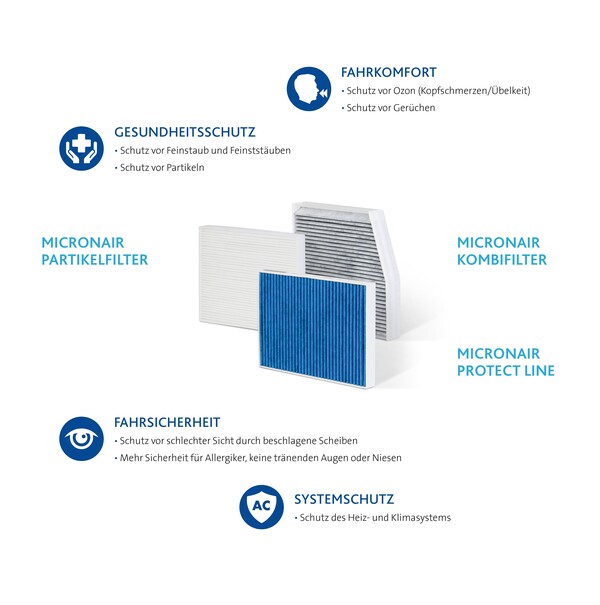
Pollen, Ruß, Feinstaub, Allergene und Gase sind bedeutende Risikofaktoren für die eigene Gesundheit und Sicherheit im Straßenverkehr. micronAir® Kfz-Innenraumfilter bieten Schutz für Menschen im Fahrzeuginnenraum und Systemprozesse. (Bildquelle: Freudenberg Filtration Technologies)
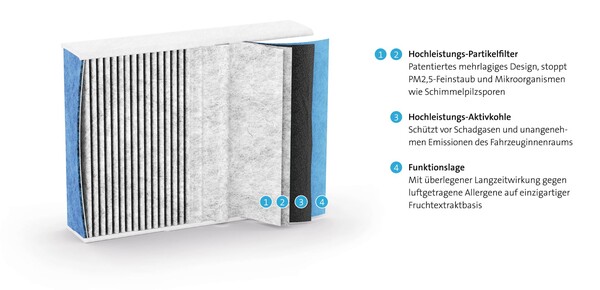
Die Kfz-Innenraumfilter der micronAir® proTect line basieren auf einem neuartigen Materialdesign mit vier Filterschichten, das unterschiedliche Filtereigenschaften kombiniert. (Bildquelle: Freudenberg Filtration Technologies)
Filter sind eine Art Mülldeponie. Sie müssen überall auf der Welt funktionieren: In trockenen, feuchten, kalten und heißen Umgebungen. In ihnen sammeln sich Staub und Gase, mitunter sind sie toxisch. Pfiffige Filteraufbauten, Polymerfaserkombinationen und Eigenschaften machen es möglich hohe Standzeiten von Kfz-Innenraumfiltern und energie- und ressourcenschonende Industriefiltern zu realisieren. Noch bessere Abscheidung und Adsorption von Gasen stehen neben der steigenden Anforderung an Zusatzfunktionen wie anti-virale Eigenschaften nach wie vor im Fokus der Entwickler. Größere Bauräume für Kfz-Innenraumfilter, wie sie teilweise bei einigen Elektrofahrzeugen realisiert werden, erlauben es beispielsweise zukünftig, die Leistung der Filter noch weiter zu steigern und damit die Luftqualität im Fahrzeuginnenraum deutlich zu verbessern.
Autor: Volker Bräunling, Global Technical Director Automotive Filter bei Freudenberg Filtration Technologies
Redaktionelle Bearbeitung: Maren Mielck, GDCh
Kommentare
Keine Kommentare gefunden!