Mit polymeren Werkstoffen zum COVID-19-Impfstoff
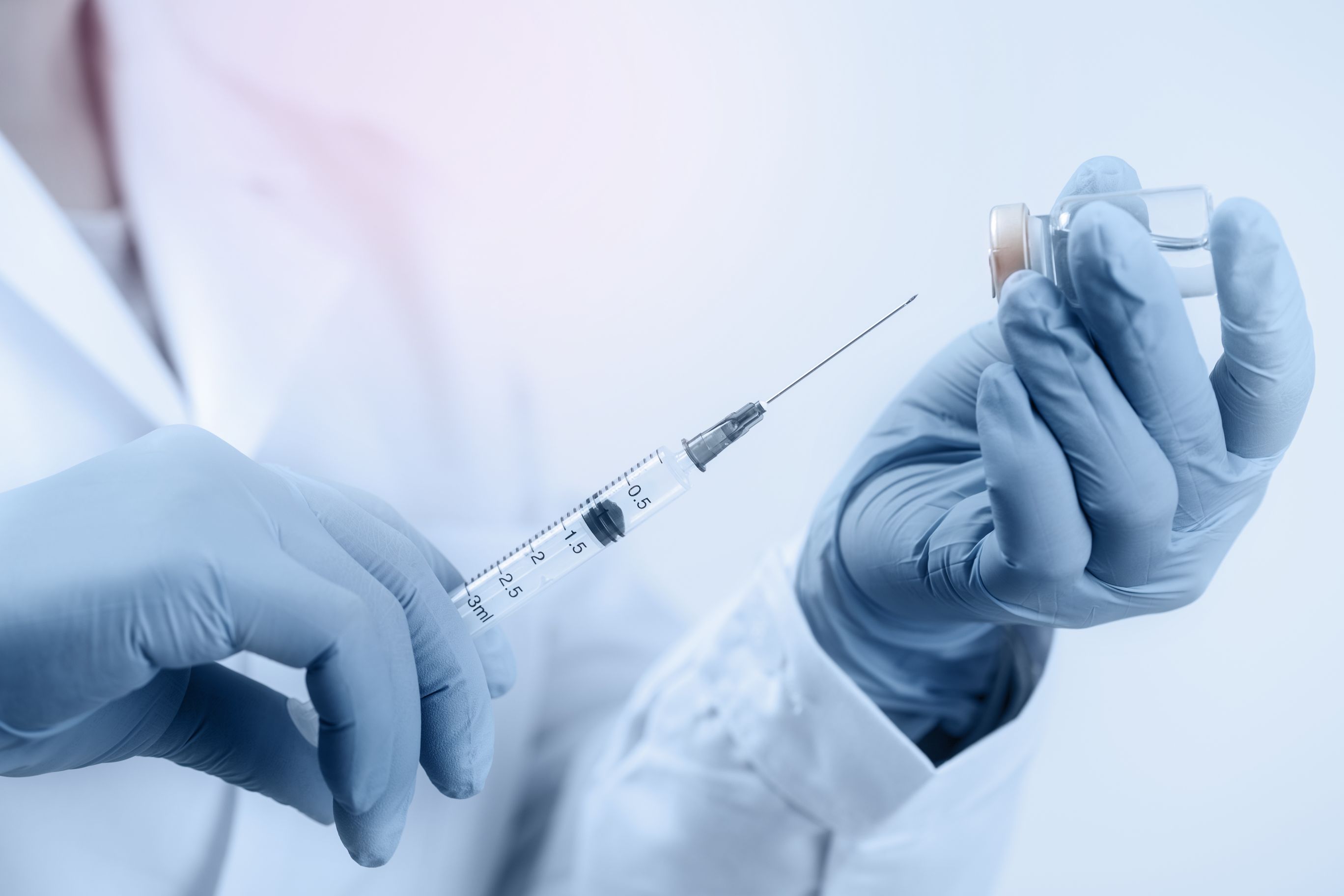
100 Jahre Makromolekulare Chemie
Seit einigen Monaten hält das Sars-CoV-2-Virus die Welt in Atem. Die Pandemie führt nicht nur zu unzähligen Todesopfern, sondern auch zu massiven wirtschaftlichen und gesellschaftlichen Verwerfungen. Als zentraler Schlüssel zur Beendigung der Krise gilt ein allgemein zugänglicher COVID-19-Impfstoff. Dieser Impfstoff muss drei Kriterien erfüllen: Eine kurzfristige Verfügbarkeit, sehr hohe Produktionsmengen und ein Preis, der den Impfstoff auch für wirtschaftlich schwache Staaten erschwinglich macht.
Unterschiedliche Ansätze für einen geeigneten Kandidaten
Anfang Juni gab es nach Angaben der Weltgesundheitsorganisation (WHO) weltweit 133 Projekte zur Entwicklung eines solchen Impfstoffes, zehn Kandidaten befinden sich bereits in klinischen Prüfungen. [1] Die Projektteams verfolgen dabei ganz unterschiedliche Ansätze: Einige Kandidaten basieren auf inaktivierten Viren oder virusähnlichen Partikeln, andere sind DNA- oder RNA-basiert. Allen Kandidaten gemein ist ein aufwendiger biopharmazeutischer Produktionsprozess, in dem die wirksame Komponente des Impfstoffes hergestellt und aufgereinigt wird.
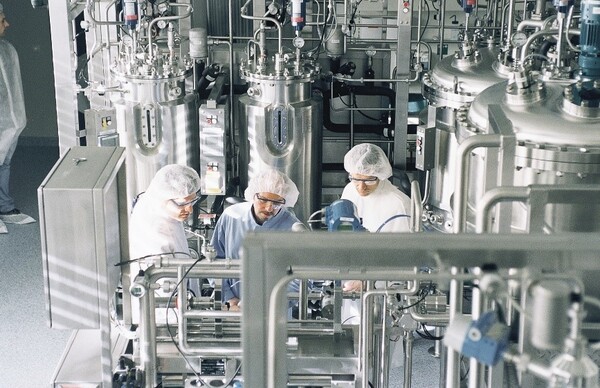
Abb. 1: Konventionelle Produktion von Impfstoffen und Biopharmazeutika in Edelstahl-Fermentern. © Sartorius Stedim Biotech GmbH
Konventionell werden solche biotechnologischen Prozesse in großen Edelstahlanlagen durchgeführt, deren Planung, Installation und Inbetriebnahme oft Jahre dauern und mit hohen Kosten einhergehen. Auch der Betrieb dieser Anlagen ist ressourcenintensiv, etwa weil alle Komponenten vor Verwendung aufwendig gereinigt und sterilisiert werden müssen. [2] Entsprechend aufwendig ist auch die Umstellung solcher Anlagen auf die Fertigung eines anderen Produktes.
Sterile Einweg-Reaktoren zur Herstellung
In den letzten Jahren hat daher ein Ansatz immer mehr an Bedeutung gewonnen, der sicher auch auf dem Weg zum COVID-Impfstoff einen entscheidenden Beitrag leisten wird: Die Verwendung von Einweg-Bioreaktoren, -Filtern und -Zubehörteilen aus Kunststoff. Was in Zeiten der Zero Waste-Bewegung zunächst seltsam anmutet, hat in der Entwicklung und Herstellung von Impfstoffen erhebliche Vorteile: Ganze Bioreaktoren mit Rührer, Sensoren und diversen Anschlüssen werden dem Kunden steril geliefert und sind sofort einsatzbereit. Gleiches gilt für Filtrationseinheiten oder Beutel zur Aufbewahrung steriler Lösungen.

Abb. 2: Einweg-Bioreaktor auf Polymerbasis: Der zentrale Teil des Reaktors wird gebrauchsfertig geliefert und nur einmal verwendet. Die nicht-produktberührende Hülle des Reaktors ist weiterhin aus Edelstahl und kann flexibel eingesetzt werden. © Sartorius Stedim Biotech GmbH
Die Hersteller gewinnen dank dieser Einwegtechnologien massiv an Flexibilität und können ihre Produktion relativ einfach auf neue Produkte wie einen Impfstoff gegen Sars-CoV-2 umstellen. Gleichzeitig müssen nur noch wenige, vielseitig verwendbare Investitionsgüter angeschafft werden, was zu einer wesentlichen Reduzierung der Kosten führt. Soll ein Prozess stufenweise vom Labor- in den Produktionsmaßstab übertragen werden, ist dies relativ leicht umzusetzen, da die Einmalreaktoren in verschiedenen Größen von einigen Millilitern bis in den Kubikmetermaßstab verfügbar sind. Auch die Produktsicherheit profitiert: Dadurch, dass medienberührende Teile nicht wiederverwendet werden, ist eine Kontamination mit anderen Produkten ausgeschlossen.
Anforderungen an das Material
Um Polymere in einem so sensiblen Umfeld wie der Impfstoffherstellung einsetzen zu können, sind bei der Entwicklung und Herstellung zahlreiche technische und regulatorische Anforderungen zu berücksichtigen. So können polymere Materialien in Kontakt mit einer Prozesslösung grundsätzlich Substanzen abgeben (sogenannte Leachables) oder durch Adsorption aus der Lösung aufnehmen. Ziel des Produktdesigns ist es immer, beide Effekte auf ein Minimum zu reduzieren. Bei den Leachables ist es außerdem wichtig, die Herkunft, Menge und Wirkung der einzelnen Substanzen zu verstehen. Produktzusammensetzung und Herstellprozess können dann so gestaltet werden, dass keine kritischen und nur Spuren unkritischer Stoffe abgegeben werden können.
Bei der Adsorption kommt es auf die Oberflächeneigenschaften der Polymere an. Viele industriell verwendete Polymere wie Polypropylen (PP) oder Polyvinylidenfluorid (PVDF) besitzen eine wasserabweisende (hydrophobe) Oberfläche und neigen deswegen dazu, hydrophobe Bestandteile aus Prozesslösungen an sich zu binden. Wird beispielsweise eine Proteindispersion über eine hydrophobe Filtrationsmembran filtriert, wird sich ein Teil dieser Proteine auf der Membran absetzen und ist damit für den weiteren Prozess verloren.
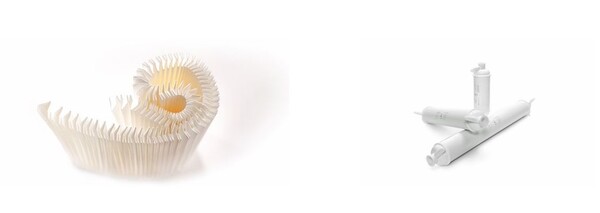
Abbildung 3: Plissierte Filtrationsmembran auf Polymerbasis (links). Die Membranen werden in Filterkapsulen verbaut (rechts), steril ausgeliefert und können sofort eingesetzt werden. Auch ganze Filtersets mit Schläuchen und Beuteln zur Aufbewahrung von Flüssigkeiten können gebrauchsfertig bereitgestellt werden. © Sartorius Stedim Biotech GmbH |
Um diesen Effekt zu vermeiden, sind zwei Strategien bekannt: Entweder wird der hydrophobe Membranfilter mit einer dünnen Schicht aus einem hydrophilen Polymer modifiziert oder es wird von vornherein eine Membran aus einem hydrophilen Polymer eingesetzt. Industriell etabliert ist der Einsatz von Cellulosemembranen, etwa zur Abtrennung von Zellen, Viren oder Proteinen. Cellulose ist von Natur aus völlig hydrophil und neigt damit nicht zur Adsorption. Dadurch lassen sich bei der Filtration besonders hohe Ausbeuten erzielen und die Filter verblocken langsamer. Ein weiterer Vorteil: Bei Cellulose handelt es sich um einen regenerativen, aus Pflanzen gewonnenen Rohstoff, der dauerhaft in großen Mengen zur Verfügung steht.
Herausforderung Nachhaltigkeit
Auch abseits der Cellulosemembranen spielt die Frage der Nachhaltigkeit eine immer größere Rolle. Mit dem Anfang des Jahres unterzeichneten European Plastics Pact haben sich erstmals Unternehmen, auch aus dem Bereich der Biotechnologie, mit dem Ziel zusammengeschlossen, den Einsatz von synthetisch hergestelltem Neuplastik zu verringern und möglichst geschlossene Stoffkreisläufe zu etablieren. Angesichts der hohen Anforderungen an Impfstoffe und Arzneimittel, insbesondere aus Perspektive der Patientensicherheit, zeichnet sich hier eine spannende und anspruchsvolle Herausforderung für Polymerchemiker und Ingenieure ab. Aber schon heute haben viele Einwegprodukte in der Biotechnologie einen kleineren ökologischen Fußabdruck als ein entsprechendes Mehrwegprodukt – und sie leisten einen entscheidenden Beitrag zur Eindämmung der Corona-Pandemie.
Autoren: Dr. Jakob Tolk und Dr. Annette Reiche (beide Sartorius Stedim Biotech GmbH)
Redaktionelle Bearbeitung: Lisa Süssmuth, GDCh
Kommentare
Keine Kommentare gefunden!