Leicht und beständig: Polymere im Leichtbau
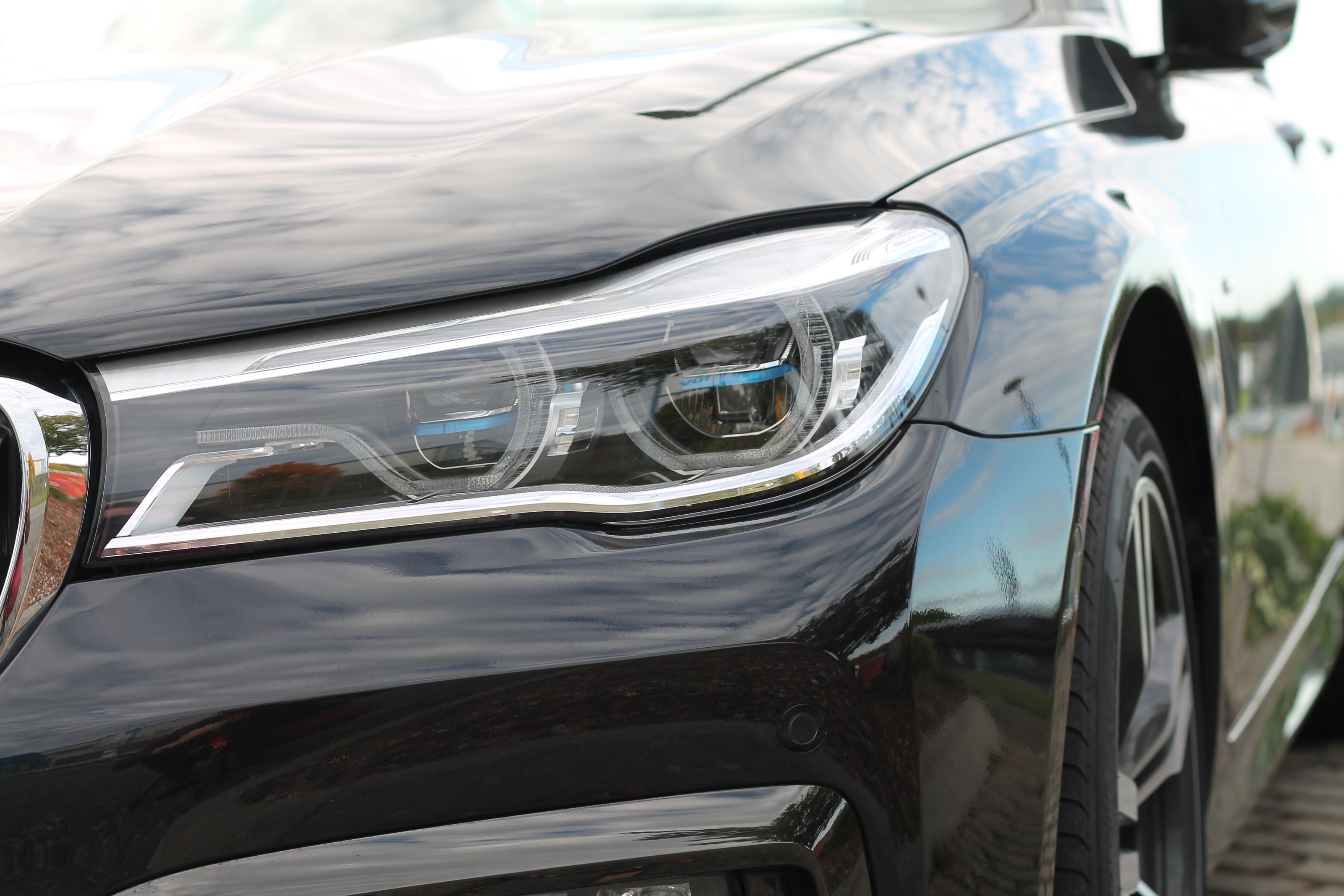
100 Jahre Makromolekulare Chemie
Seit Jahrzehnten dringen Kunststoffe in diverse Wirtschaftszweige vor und sind aus vielen Bereichen und Anwendungen nicht mehr wegzudenken. Kunststoffe ermöglichen beispielsweise eine effiziente Agrarindustrie und eine klimaschonende Dämmung im Bauwesen. Doch auch in Hochleistungsanwendungen der Elektrik-/Elektronik- sowie der Automobilindustrie hat Kunststoff zunehmend Einzug gehalten. Diese Erfolgsgeschichte wurde begleitet von diversen Innovationen aus der Kunststoff- und Chemieindustrie, die die aktuellen Entwicklungen und Anwendungen überhaupt erst möglich machen konnten. Im folgenden geben wir einen Überblick über die Rolle von Kunststoffen im Leichtbau.
Wie Kunststoffe Leichtbau ermöglichen
Die Verarbeitungsprozesse von Kunststoffen bieten meist eine hohe Designfreiheit, eine gute Reproduzierbarkeit sowie Wirtschaftlichkeit. Zudem besitzen die Materialien eine geringe Dichte. Diese Kombination ermöglicht ein Potenzial für die Kunststoffe im Leichtbau, das für typische Anwendungen im Bereich von etwa 20 bis 30 Prozent im Vergleich zur konventionellen Bauweise liegt. Die Kunststoffe ersetzen in diversen Branchen andere Konstruktionswerkstoffe wie zum Beispiel Metalle oder Glas: Darunter die Automobilscheinwerfer – früher aus Glas und heute stets aus Polycarbonaten.
In den vergangenen Jahren wurde der Leichtbau mithilfe von Polymeren im Wesentlichen durch drei neue Technologien vorangetrieben:
- Hochverstärkte Kunststoffe für den Spritzgießprozess: hohe Steifigkeiten und Festigkeiten durch hohe Anteile (bis 60 Gewichtsprozent) an Verstärkungsfasern, ermöglicht durch leichtfließende thermoplastische Basisharze
- Kunststoff/Metall-Hybride: synergetische Verbindung der hohen Steifigkeit von Metallen, mit der geringen Dichte, der hohen Produktivität und Gestaltungsfreiheit sowie den geringeren Kosten von Kunststoffen
- Endlosfaserverstärkte Kunststoffe: gerichtete Einbringung von Endlosfasern entlang der Hauptlastpfade. Erstmalige Großserienfertigung durch Nutzung von thermoplasti-schen Matrixsystemen in vollautomatisierten Systemen
Hochgefüllte Kunststoffe
Eine derartige Innovation im Leichtbau sind hochverstärkte Polyamid 6-Typen, wie das Durethan® BKV60H2.0EF DUS060, das einen Glasfaseranteil von 60 Gewichtsprozent besitzt. Dadurch sind die Materialien beispielsweise für Bauteile geeignet, die eine große Belastung aushalten sollen. Weitere Eigenschaften wie eine geringe Wärmeausdehnung und Wasseraufnahme nähern diese Kunststoffe in ihren Eigenschaften den Metallen an.
Damit die hochgefüllten Werkstoffe in konventionellen Verfahren wie dem Spritzgießen verarbeitet werden können, muss die Matrix speziell weiterentwickelt werden. Die Fließeigenschaft wird so angepasst, dass sie der von geringer verstärkten Werkstoffen mit 30 Prozent Glasfasern ähnelt oder diese gar übertrifft. Dadurch können die Materialien trotz des hohen Glasfasergehalts auch bei geringen Wanddicken reproduzierbar und prozesssicher verarbeitet werden. Der automobile Leichtbau setzt seit Jahren die hochgefüllten glasfaserverstärkten Kunststoffe ein.
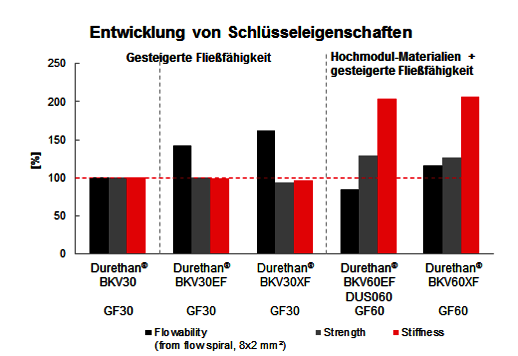
Ein Vergleich der wesentlichen Materialeigenschaften zwischen einem Polyamid 6 mit einem 30 prozentigen Glasfaseranteil (links) und mit 60 Prozent Glasfaseranteil (rechts). Es werden die Fließfähigkeit (schwarz), die Festigkeit (grau) und die Steifigkeit (rot) verglichen. © LANXESS Deutschland GmbH
Hybride aus Kunststoff und Metall
Diverse Anwendungen, zum Beispiel im Automobilbau, erfordern besonders hohe Steifigkeiten und Festigkeiten einzelner Bauteile. Diese Eigenschaften können teils selbst von hochgefüllten Compounds nicht erreicht werden. Um trotzdem die Vorteile von Kunststoffen hinsichtlich Designfreiheit und Produktivität nutzen zu können, wurden hybride Materialsysteme aus Kunststoff und Metall entwickelt. In den 1990er-Jahren wurde die Technologie von einer Nischentechnologie bis zum Industriestandard weiterentwickelt und verbreitet. Zu den Pionieren, welche die Entwicklung der Kunststoff/Metall-Hybride geprägt haben, zählt zum Beispiel LANXESS. Eine Kernanwendung für diese Hybride sind die sogenannte Frontends – sicherheitsrelevante Strukturbauteile in der Front von Fahrzeugen, die hohen Belastungen standhalten müssen. Nach ersten Entwicklungen automobiler Frontends in den 1990er-Jahren, werden sie heute weltweit millionenfach als Kunststoff/Metall-Hybride hergestellt. Darüber hinaus finden wir sie auch in Automobilpedale und Dachspriegel.
Neue Entwicklungen im Bereich der Kunststoff/Metall-Hybride zielen auf Anwendungen ab, bei denen besonders hohe Anforderungen hinsichtlich Torsionssteifigkeit und -festigkeit vorliegen. Ein typisches Beispiel ist der Instrumententafelträger, das Rückgrat des gesamten Cockpits eines Autos. Dieser muss vor allem hohe Eigenfrequenzen erzielen, um damit Vibrationen wie des Lenkrads zu minimieren.
Zum Beispiel vereinfacht eine aktuelle Entwicklung der Firma LANXESS die Herstellung der Kunststoff/Metall-Verbundbauteile. Metallische Hohlprofile werden auf einer Standardspritzgießmaschine mithilfe von Kunststoff funktionalisiert. Der dabei erzeugte Formschluss ermöglicht es, hohe Kräfte zu übertragen. Er soll als Instrumententafelträgers angewendet werden.
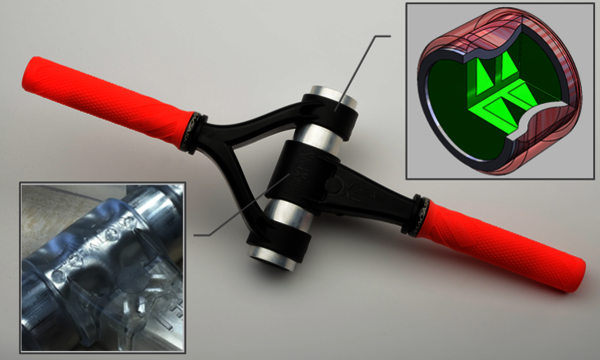
Technologiedemonstrator bestehend aus einem metallischen Hohlprofil, welches mittels Kunststoff funktionalisiert wurde (in der Mitte Polyamid 6 GF60, Durethan® BKV60H2.0 EF, links transparentes Polycarbonat) © LANXESS Deutschland GmbH
Endlosfaserverstärkte Kunststoffe
Anwendungen der endlosfaserverstärkten Kunststoffe sollen die Anisotropie und die hervorragenden mechanischen Eigenschaften entlang der Fasern nutzen, zum Beispiel das thermoplastischen Matrixsystem. Die thermoplastische Matrix kann in integrierten Prozessen verarbeitet werden, die die Großserienfertigung möglich machen. Dem bedienen sich unter anderem Luft- und Raumfahrt sowie der Automobilbau, aber auch der Leichtbau für Laptopcover oder Handyschalen. Diese erfordern hohe optische Anforderungen, sollen aber auch leicht sein.
Kunststoffbasierter Leichtbau in der Zukunft
Der Leichtbau wird auch in Zukunft eine zentrale Rolle in vielen Entwicklungen spielen. Dabei wird sich jede Leichtbaumethodik hinsichtlich der Recyclingmöglichkeiten und werkstofflicher und energetischer Bilanzen verantworten müssen. Dem daraus entstehenden Zielkonflikt zwischen Leichtbau und Recycling kann nur mithilfe von innovativen Technologien begegnet werden, wie sie in den vergangenen Jahrzehnten erarbeitet wurden. Im zunehmend internationalen Wettbewerb werden Technologien für den Leichtbau auf Basis von Kunststof-fen sowie deren Weiterentwicklung daher auch in Zukunft eine Möglichkeit darstellen, die jeweilige Marktposition für sich zu behaupten und zu festigen.
Autoren: Dr.-Ing. Matthias Theunissen, Dr.-Ing. Martin Wanders (High Performance Materials, LANXESS Deutschland GmbH)
Redaktionelle Bearbeitung: Lisa Süssmuth, GDCh
Titelbild: Lignum-Solutions/stock.adobe.com
Kommentare
Keine Kommentare gefunden!