Kautschukblends lösen Zielkonflikte – Teil 2: Praktische Anwendungen

100 Jahre Makromolekulare Chemie
Blendtechnologie wird mit dem Ziel eingesetzt, Elastomere mit gewünschten Eigenschaftskombinationen herzustellen, die aus einzelnen Kautschuken nicht herzustellen sind. Durch die Variation der Zusammensetzung der Blends werden die Eigenschaften den Anforderungen der Anwendung angepasst. Somit sind die Anwendungsmöglichkeiten für Kautschukblends um einiges breiter als die der einzelnen Kautschuke, welche die Grundlage für diese Technologie bilden [1].
Grundsätzlich lassen sich die am Markt befindlichen Kautschuke beliebig miteinander zu binären oder ternären Blends vermischen. Dem Entwickler von neuen Elastomerwerkstoffen sind (fast) keine Grenzen gesetzt. Hinzu kommen noch Blends von Kautschuken mit Kunststoffen, die als „thermoplastische Vulkanisate“ eine separate Werkstoffklasse darstellen und einen wichtigen Markt abdecken.
Für die Umsetzung der im ersten Teil eingeführten theoretischen Konzepte gilt, dass die Materialparameter der Komponenten, eine adäquate Mischtechnologie und eine effiziente Vernetzung der Blends zu einer definierten Phasenmorphologie führen, die das gewünschte Leistungsspektrum garantiert. Das potentiell verbesserte Leistungsprofil der Kautschukblends umfasst physikalische und chemische Aspekte, die je nach Phasenmorphologie und ausgewählten Komponenten zum Tragen kommen.
Ein Vorteil der Blendtechnologie ist, dass hierfür eingeführte Mischverfahren genutzt bzw. angepasst werden können. Somit können Kautschukverarbeiter nicht nur die existierenden Rohstoffe, sondern auch den zur Verfügung stehenden Maschinenpark nutzen, um innovative Werkstoffe herzustellen.
Ob als mehrphasige oder einphasige Systeme wird von vernetzten Kautschukblends eine breite Palette von Endeigenschaften abgedeckt. In zweiphasigen Blends sorgen autonome Domänen mit spezifischen physikalisch-chemischen und mechanischen Eigenschaften, die denen der originären Blendkomponenten entsprechen, die gewünschten Eigenschaftskombinationen auf das Blend übertragen werden. Einphasige Blends hingegen, die sich über thermodynamische Mischbarkeit bilden, haben neue Eigenschaften. Sie zeichnen sich durch eine einfachere Verarbeitung und eine mechanische Integrität der vernetzten Blendsysteme aus.
Mit steigender Dispersion beim Mischen unverträglicher Kautschuke nimmt die Zugfestigkeit und die Bruchenergie der gefertigten Vulkanisate zu. Wie aus Abb. 1 ersichtlich ist, nehmen nicht nur die Materialwerte der Vulkanisate, sondern auch ihre Schwankungen mit der Mischzeit als Folge der ansteigenden Grenzschicht im Material zu.
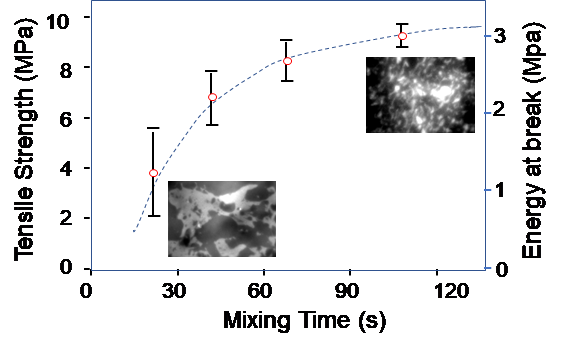
Abb.1 Entwicklung der Zugfestigkeit und Bruchenergie eines NR/SBR (50/50) Blends mit der Mischzeit [2]
(Abbildung: Deutsches Institut für Kautschuktechnologie e. V. (DIK e. V.))
Bei stark unverträglichen Blends (hohe δ-Parameterdifferenz) sind die Domänen auch nach langem Mischen immer noch zu hoch, um gute physikalische Eigenschaften zu garantieren. Dies ist insbesondere bei Blends aus Komponenten mit unterschiedlicher Polarität und unterschiedlichem Sättigungsgrad der Fall. Die hohe Grenzflächenspannung bewirkt eine geringe Phasenanbindung und damit ungünstige mechanische Festigkeitseigenschaften. Um aus NBR-Kautschuk und EPDM-Kautschuk einen öl- und alterungsbeständigen Kautschukblend mit ausreichender Zug- und Weiterreißfestigkeit herzustellen, sind Phasenvermittler erforderlich.
Die Zugabe von Phasenvermittlern wird die Dispersion der Phasen beschleunigt und die Grenzflächenspannung herabgesetzt, was im stationären Mischbetrieb die mittlere Domänengröße signifikant verkleinert, ohne zu einem Phasenübergang zu führen. Von praktischer Bedeutung sind die Verbesserung der Zugfestigkeit und der Bruch-dehnung, womit die technische Nutzung des Blends steigt.
Höhermolekulare Phasenvermittler siedeln sich zwischen den Blendphasen an, wodurch die Phasenanbindung verbessert und Grenzfläche physikalisch „verstärkt“ wird. Als Phasenvermittler werden bevorzugt Blockcopolymere eingesetzt, deren Blöcke jeweils einer der Komponenten ähnlich sind. Copolymere und Homopolymere, deren δ-Parameter zwischen denen der Blendkomponenten liegt, haben eine ähnlich gute Wirkung wie Blockcopolymere, wie sich durch den Einsatz von Polyalkenylenen bei EPDM/NBR-Blends zeigt (Abb. 2).
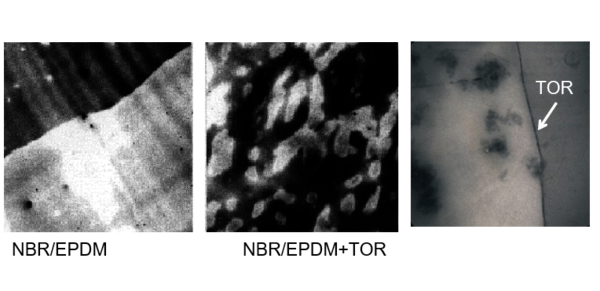
Abb. 2: Wirkung des Phasenvermittlers TOR*1 in EPDM/NBR-Blends und Anordnung entlang der Grenzfläche
(Abbildung: Deutsches Institut für Kautschuktechnologie e. V. (DIK e. V.))
Phasenvermittler entfalten ihre maximale Wirkung bei der kritischen Micellenkonzentration (cmc). Bei diesen Dosierungen werden Zugfestigkeit, Weiterreißfestigkeit und Abriebwiderstand des Blends um ein Mehrfaches erhöht.
Um die mechanischen Eigenschaften, besonders die Verschleißfestigkeit und Lebensdauer der Elastomere zu erhöhen, genügt es nicht, die Kautschuktypen zu optimieren, sondern ist unabdingbar, in die Mischungen verstärkende Füllstoffe (Ruße, Kieselsäuren) einzuarbeiten und das gesamte System effizient zu vernetzen. Bei mehrphasigen Blends kann beides zu Problemen führen, die von Materialentwicklern und Prozessingenieuren rechtzeitig erkannt werden müssen.
Je nach Affinität des eingesetzten Füllstoffes zu einer der Kautschukphasen findet eine natürliche Verteilung der nanoskaligen Partikel in den Blendphasen statt, die sich in der Folge auf die Endeigenschaften des vernetzten Kautschukblends auswirkt. [3] Ebenso ist bei Kautschuken mit unterschiedlicher Polarität mit einer selektiven Verteilung des Vernetzungssystems zu rechnen, wodurch in den Phasen eine unterschiedliche Vernetzungsdichte das mechanische Verhalten beeinflusst. Die anfänglich unbegrenzten Möglichkeiten werden so durch reale physikalisch-chemische Prozesse eingeschränkt – eine Herausforderung für Materialentwickler und Prozessingenieure.
Ein Reifen wird aus mehreren speziellen Mischungen (Lauffläche, Seitenwand, Karkasse, Wulst etc.) konfektioniert. Sie bestehen alle aus verschiedenen Kautschukmischungen, haben jedoch ein gemeinsames Merkmal. Sie sind phasengetrennt und können somit verschiedene Funktionen abdecken. Moderne Reifenlaufflächen sind das Ergebnis einer langen Optimierungskette, um die Traktion (Haftung), den Abriebwiderstand und Rollwiderstand auf das heute geforderte Niveau zu bringen. Diese Entwicklung hat über mehr als ein halbes Jahrhundert Innovationen in der Kautschuksynthese, in der Morphologie und Aktivität der Füllstoffe und der Technologie der Kautschukmischungen und Füllstoffdispersion ausgelöst.
In abgestimmten Mengenverhältnissen werden für PKW-Laufflächen Kautschuke mit unterschiedlicher Kettenbeweglichkeit und Dämpfungseigenschaften eingesetzt, um Abriebwiderstand und Traktion zu optimieren. Den höchsten Abriebwiderstand garantieren Kautschuke mit der höchsten Kettenbeweglichkeit (niedrigster Tg), die vorzugsweise auch unter Dehnung kristallisieren. Diese Aufgabe wird von hoch cis-1,4-Polybutadienen erfüllt, die über Koordinationskatalyse (Ziegler-Natta und Metallocene) synthetisiert werden. Abhängig von dem eingesetzten Katalysator steigt der 1,4-cis-Gehalt im Polymeren in der Reihenfolge der zentralen Metalle des Katalysators [4]:
Ti < Co < Ni < Nd
In der gleichen Reihung nehmen Schmelzpunkt der kristallinen Bereiche und der Abriebwiderstand zu.
Die notwendige Straßenhaftung und Traktion erfordert je nach Geschwindigkeit des Fahrzeugs eine Energiedissipation des Kautschuks bei Frequenzen im MHz-Bereich.
Dazu werden unpolare Kautschuke mit einer Tg um -40 bis -10°C erforderlich, idealerweise die breit aufgestellte Gruppe der Emulsions- und Lösungs-SBR. Durch Variation der Styrol- und Vinyleinheiten können bei L-SBR die Tg dieser Kautschuke fast beliebig variiert werden. Somit trägt die Kettenarchitektur (Microstruktur) des Kautschuks maßgeblich dazu bei, eine Feineinstellung der Traktion zu ermöglichen.
Rollwiderstand geht auf eine niederfrequente Energiedissipation zurück, die von der Stärke des gebildeten Füllstoffnetzwerkes und damit der Mikrodispersion des Füllstoffes abhängt. Auch hier hilft ein Kautschuk mit guter Wechselwirkung zum jeweilig gewählten Füllstoff (z. B. SBR mit höherem Styrolanteil) Die Verwendung von funktionalisiertem L-SBR oder E-SBR führt einer verbesserten Kieselsäuredispersion und damit zu einem niedrigeren Rollwiderstand in modernen Silika-SBR/BR-Laufflächen.
Bei dynamisch hoch belasteten LKW-Reifen liegen die Schwerpunkte auf dem Abriebwiderstand und dem Ausbruch von Laufflächenstollen. Folgerichtig enthalten LKW-Reifen Naturkautschuk (NR), der unter Dehnung kristallisiert und die höchste Weiterreißfestigkeit unter den Kautschuken zeigt in Kombination mit BR und SBR.
Für Reifenanwendung werden bevorzugt Mischungen im Phasenumkehrgebiet verwendet. Die Kautschuktypen und die Mengenverhältnisse werden der vorhandenen Prozesstechnik angepasst und können nach dem Einsatzzweck des Reifens variabel gestaltet werden.
Es wird häufig versucht, einen teuren Rohkautschuk mit einem billigeren Produkt zu verdünnen, ohne an der spezifischen Funktion einzubüßen. So wird bei Innerlinern aus Butylkautschuk (IIR, CIIR) versucht, einen Teil des gasundurchlässigen IIR oder CIIR mit billigerem NR zu substituieren. Gleichermaßen wird versucht, die Alterungs- und Ozonbeständigkeit von EPDM mit geringen Volumina von NR zu erhalten.
Untersuchungen von Transportprozessen in Spezialkautschukblends zeigen: Solange der Spezialkautschuk (IIR, EPDM, NBR etc.) die kontinuierliche Phase bildet, nimmt die Zielgröße (Ozonbeständigkeit, Permeation, Ölbeständigkeit, etc.) in einem geringen Maße zu. (Abb. 3).
Wird das Phasenumkehrgebiet überschritten, sind die Kautschukblends außerhalb der gesetzten Spezifikation.
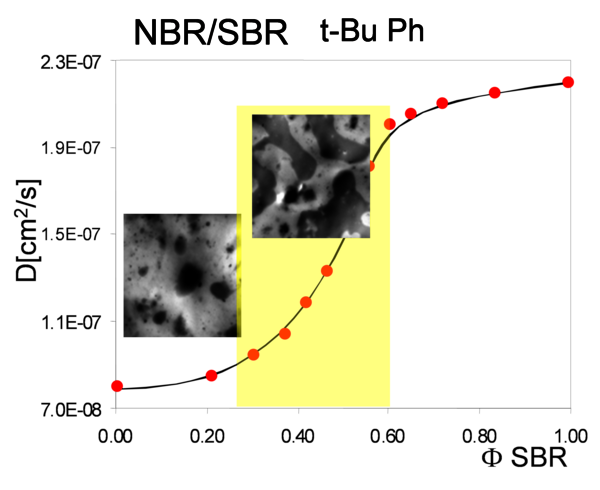
Abb. 3: Diffusionkoeffizient von t-BuPh in NBR/SBR Blends [5]
(Abbildung: Deutsches Institut für Kautschuktechnologie e. V. (DIK e. V.))
Herausforderungen
Aufgrund der unterschiedlichen Kautschuk-Füllstoff-Wechselwirkung wird der Füllstoff beim Mischen präferentiell in die Blendphasen verteilt, wodurch sich die rheologischen Eigenschaften der Mischung und vor allem die physikalischen Eigenschaften der vernetzten Kautschukblends ändern.
Wird der Mischvorgang in konventioneller Weise durchgeführt, kommt es zu einer natürlichen Füllstoffverteilung, die von der Kautschuk-Füllstoff-Wechselwirkung und den Temperaturbedingungen im Mischer vorgegeben ist. Um die Verteilung des Füllstoffs technisch zu steuern, können sogenannte Masterbatches mit definierten Füllstoffanteilen in einer der Blendphasen vor der eigentlichen Blendherstellung gemischt werden. Die Verteilung des Füllstoffs wird so eingestellt, dass der Kautschuk, der eine höhere Verstärkung benötigt, auch den höheren Anteil erhält. Zusätzlich zu der Auswahl der Blendpartner werden durch geeignete Füllstoffverteilung die Hysterese und damit die Wärmebildung minimiert oder die Zugfestigkeit und die Lebensdauer maximiert. Allein durch einen höheren Anteil von silanisierter Kieselsäure in der SBR/BR Phase wird die Lebensdauer von NR/SBR/BR-Verschnitten signifikant erhöht (Abb. 4).
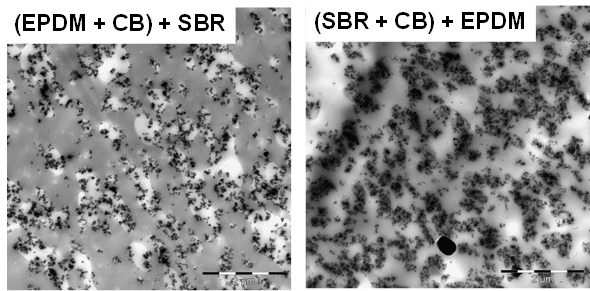
Abb. 4: Erzwungene Füllstoffverteilung durch Masterbatchtechnologie
(Abbildung: Deutsches Institut für Kautschuktechnologie e. V. (DIK e. V.))
Wird der Ruß in EPDM vorgegeben, kann er während des Mischens fast quantitativ von dem SBR übernommen werden. Umgekehrt kann der Ruß aufgrund der guten Wechselwirkung mit SBR nicht in die EPDM-Phase transferiert werden.
Die Wirkung der Füllstoffverteilung wird vor allem bei dynamischen Eigenschaften und bruchmechanischen Eigenschaften beobachtet. Überfüllte Kautschukphasen zeigen eine überhöhte Erwärmung bei dynamischer Dauerbelastung. Bei der dynamischen Rissfortpflanzung muss durch den höheren Füllstoffanteil dafür gesorgt werden, dass der Kautschuk, der die geringere Festigkeit hat, verstärkt wird (Abb. 5).
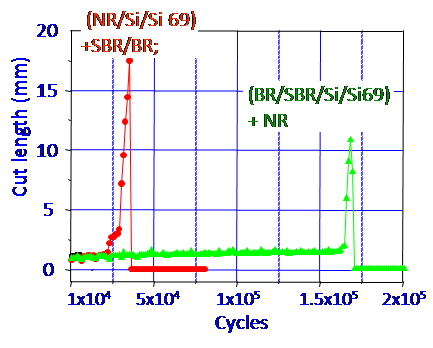
Abb. 5: Einfluss der Füllstoffverteilung auf das Risswachstum von NR/SBR/BR-Blends
(Abbildung: Deutsches Institut für Kautschuktechnologie e. V. (DIK e. V.))
Um das Potential der verstärkenden Füllstoffe in Kautschukblends auszuschöpfen, bedarf es genauer Methoden zur Bestimmung der Verteilung, gesicherte Kenntnis zur Kautschuk-Füllstoff-Wechselwirkung und nicht zuletzt verfahrenstechnisches Können: eine komplexe interdisziplinäre Aufgabe.
Eine weitere Komplikation entsteht durch die Verteilung des Vernetzungssystems im Polymer-Blend. Dadurch werden die Phasen eines Polymer-Blends und die Grenzschicht unterschiedlich vernetzt. Dieses führt vor allem zu Einbußen der Festigkeitswerte. Die Entwicklung des geeigneten Vernetzungssystems, um eine ähnliche Vernetzungsdichte in beiden Phasen und eine wirksame Co-Vernetzung zu realisieren, gehört zu den spannenden Aufgaben eines Materialentwicklers.
Die gezeigten Beispiele sollen das Potential der Kautschukblends für die Entwicklung neuer Elastomere sowie den Forschungsbedarf aufzeigen, der auf diesem Gebiet der Kautschuktechnologie herrscht.
Der Autor: Prof. Dr. Robert H. Schuster, Ehem. Leiter des Deutschen Institut für Kautschuktechnologie, Berater für die Kautschukindustrie
Redaktionelle Bearbeitung: Maren Mielck, GDCh
Literatur:
R. H. Schuster, Angew. Makromol. Chemie 202/203 (1992) 159.
H.-M. Issel, Dissertation Universität Hannover (1993)
W. M. Hess, Ch. Herd und P. C. Vegvari, Rubber Chem. Technol., 66 (1993) 329.
D. J. Wilson, Makromol. Chem., Macromol. Symp., 66 (1993) 273.
C. Bergmann, Dissertation Leibniz Universität Hannover (2006)
Kommentare
Keine Kommentare gefunden!