Faser-Kunststoff-Verbunde: Die Verbindung zweier Welten
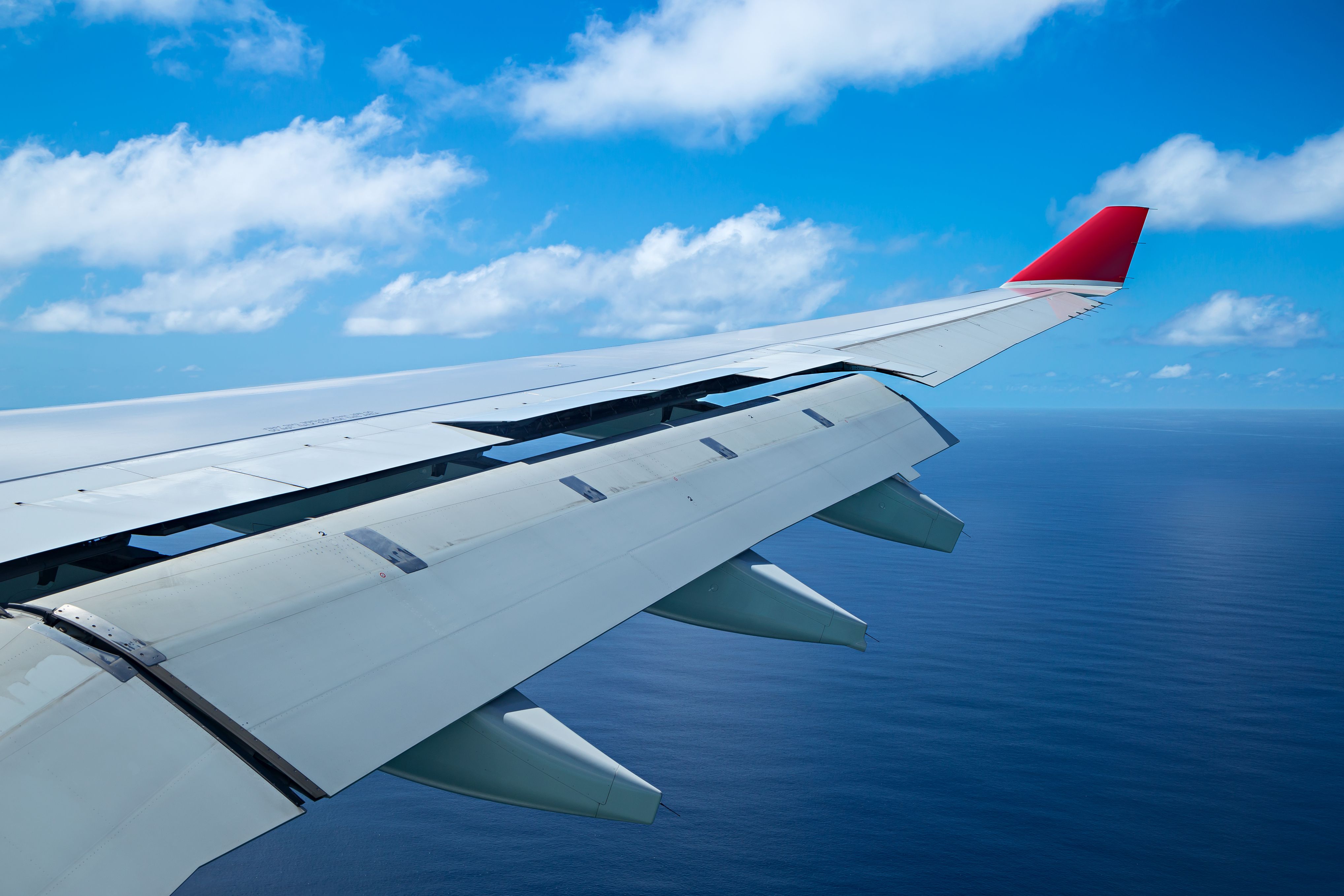
100 Jahre Makromolekulare Chemie
Preisgünstige Massenherstellungsverfahren ermöglichten den Siegeszug der Kunststoffe in nahezu alle Lebensbereiche und Anwendungen, vom Autositz über die Zahnbürste bis hin zum Computertomographen.
Dabei können diese Allroundmaterialien in drei große Gruppen unterteilt werden. Während Thermoplaste und Elastomere oft aufgrund der einfachen Herstellungsmöglichkeiten im alltäglichen Leben zu finden sind, sind Duromere meist in Spezial- und Nischenanwendungen anzutreffen. Das liegt vor allem daran, dass Moleküle mit Reaktivgruppen nach der Formgebung erst „vernetzt“ werden müssen, um eine Formstabilität zu gewährleisten – man spricht hier von sogenannten Reaktivharzen.
Die Einsatztemperatur reicht dann oft über 250 °C hinaus, ein Bereich in dem herkömmliche Elastomere und Thermoplaste bereits deutlich ihre thermische Belastungsgrenze überschritten haben. Außerdem prädestiniert die ausgezeichnete Chemikalien- und UV-Beständigkeit, Duromere für Außenanwendungen. Einen besonderen Marktanteil haben Harze in der Konstruktion von verschiedenen technischen und lasttragenden Bauteilen. In Kombination mit Verstärkungen aus Glas- oder Kohlenstofffasern werden „GFK“ und „CFK“ als Faser-Kunststoff-Verbundebezeichnet. Diese Fasern sind mit einem Durchmesser von 5-18 µm dünner als ein menschliches Haar und haben herausragende mechanische Eigenschaften.
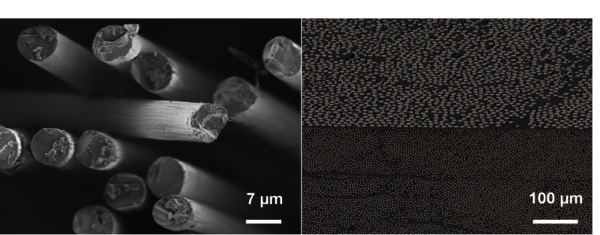
Abbildung 1: Bilder vom Rasterelektronenmikroskop. Links: Kohlenstofffasern mit einem Durchmesser von 7 µm – ein menschliches Haar ist 10x dicker; Rechts: Kohlenstofffasern unterschiedlich ausgerichtet in einem CFK Bauteil. © F. Hübner, F. Schönl, V. Altstädt
Verwendung im Leichtbau
Wurden im 19. Jahrhundert bereits Kohlenstofffasern zur Anwendung als Glühbirnendraht hergestellt, entdeckte man erst lange Zeit später deren Potential als Verstärkungsmaterial. Seit Ende der 1960er Jahre stellte man dann Kohlenstofffasern für viele Branchen wie die Luftfahrt, Automobilindustrie, und Windenergie her. Allerdings war aufgrund der damaligen extrem hohen Preise von über 1500 €/kg die Anwendung der Raumfahrt vorbehalten, in der extreme Gewichtsoptimierungen benötigt wurden. Die gefragte Anwendung aufgrund des Leichtbaupotentials lässt sich vor allem durch die geringe Dichte erklären, die nur 20 % der Dichte von Stahl beträgt, bei gleichzeitig höherer Festigkeit in Faserrichtung. Die Produktionskapazitäten der Kohlenstofffasern mit über 150.000 Tonnen im Jahr 2019 ermöglichen Preise von unter 20 €/kg. Diese werden vor allem in den USA, Japan und China produziert [1]. Während heutzutage 24 % der weltweit hergestellten Kohlenstofffasern von der Automobilbranche und 13 % für Windenergie sowie 13 % für Sportanwendungen verwendet werden, liegt der Primärbedarf mit 36 % immer noch im Luft- und Raumfahrtsektor [2].
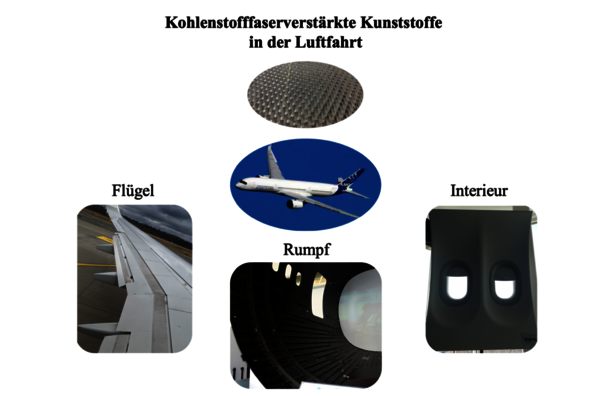
Abbildung 2: Kohlenstofffaserverstärkte Kunststoffe und deren Anwendungen in der Luftfahrt. © F. Hübner, F. Schönl, V. Altstädt
In Flugzeugen finden sie Einsatz im Innenraum der Kabine, sowie in strukturtragenden Bauteilen wie den Flügeln, dem Höhen- und Seitenleitwerk oder dem Rumpf. Moderne Langstreckenjets wie der Airbus A350 oder der Boeing 787 „Dreamliner“ bestehen aus rund 50 % Faser-Kunststoff-Verbunden, was dazu führt, dass der Kerosinverbrauch sogar bei maximalem Abfluggewicht im Vergleich zu herkömmlichen Flugzeugen auf ein bisher nicht erreichtes Minimum sinkt [3].
Die Hauptaspekte in der Materialforschung liegen heutzutage neben der benötigten hohen mechanischen Festigkeit auch in der gleichzeitigen Zähigkeit des Materials. Duromere wie Epoxid- oder Phenolharze haben durch die hohe Festigkeit den Nachteil, dass sie auch sehr spröde sind, was bei wechselnder Belastung bei kalter Umgebungsluft während dem Flug zur Rissausbreitung führen kann. Um dem vorzubeugen, werden Zusatzstoffe (Additive) wie kleinste hochzähe Kautschukpartikel bei der Herstellung verwendet, die Risse stoppen und somit ein Bauteilversagen verhindern.
Eigenschaftskombination im Verbund
Der große Vorteil der Faser-Kunststoff-Verbunde ist die positive Eigenschaftskombination von Faser, Matrix und Interphase, die für hohe mechanische Eigenschaften bei gleichzeitig geringem Gewicht sorgen. Nachteilig ist bei Kunststoffen jedoch die geringe elektrische- und thermische Leitfähigkeit sowie eine leichte Entflammbarkeit, was eine starke Rauchentwicklung und die Entstehung giftiger Gase verursacht. Dies spielt bei den strukturtragenden Faser-Kunststoff-Verbundbauteilen, wie etwa bei Flugzeugflügeln eine geringe Rolle. Allerdings verhindert dieser Nachteil den Einsatz an anderen Stellen. Deshalb bringen diese Werkstoffe trotz der Verfügbarkeit seit den 1960er Jahren immer noch ein sehr großes Forschungspotential mit sich. Über den gezielten Einsatz diverser Additive, lassen sich auch diese Nachteile beseitigen. Die Zugabe von leitfähigen Füllstoffpartikeln kann dafür sorgen, dass auch der Verbund elektrisch leitfähig wird. So wird in aktuellen Forschungsprojekten der Faser-Kunststoff-Verbund mit Kohlenstoffnanoröhrchen (CNT) modifiziert. Dadurch bildet sich eine deutlich erhöhte elektrische Leitfähigkeit im Material aus. Durch diese Neuentwicklung, könnten in Zukunft Flugzeugflügel mithilfe von aufgebrachten dünnen Schichten dieses Werkstoffs durch das Prinzip der Widerstandsheizung elektrisch erwärmt werden, wodurch eine umweltfreundlichere Enteisung der Jets vor dem Abflug im Winter erfolgen kann.
Ebenfalls lassen sich Flammschutzmittel wie etwa Phosphorverbindungen einbringen. Diese sorgen dafür, dass Bauteile im Flugzeuginnenraum erst später in Brand treten. Eine Verlängerung der Fluchtzeit für die Passagiere in Flugzeugen ist die Folge, was eine internationale Kernanforderung für das Erreichen einer Materialzertifizierung darstellt. Dies hat ebenso bei Zügen oder anderen Transportmitteln heutzutage eine große Relevanz.
Verarbeitungstechnologien gestalten den Werkstoff interessant
Zur Verarbeitung der Faser-Kunststoff-Verbundmaterialien stehen den Anwendern diverse Verarbeitungsmethoden zur Verfügung. Für große flächige Bauteile verwendet man heue vor allem das „Prepreg-Verfahren“, bei dem mit Harz getränkte Fasertextilien als Einzellagen abgelegt und anschließend bei hoher Temperatur für einige Stunden gehärtet werden. Die nachfolgende Tabelle gibt einen kurzen Überblick.
Prepregverarbeitung | ||
---|---|---|
Handlaminieren | Automatisches Tape Legen (ATL) | Automatisches Faser Platzieren (AFP) |
|
|
|
|
|
|
|
Das Handlaminieren ist das einfachste Herstellungsverfahren. Als nicht-automatisierte Technik ist die Gefahr von Qualitätsschwankungen allerdings groß und die Erfahrung der Mitarbeiter beeinflusst die Produktqualität in hohem Maße. Da jedoch keine großen Investitionskosten für Anlagen anfallen, kommt es dennoch vor allem für kleinere Serien und auch speziell für individuell gefertigte Bauteile sowie im Labormaßstab zum Einsatz. Dem gegenüber stehen die automatischen Legeverfahren wie „Automatisches Tape Legen (ATL)“ und das „Automatische Faser Platzieren (AFP)“. Je nach gewünschter Produktgröße und -geometrie (leicht oder stark gekrümmt) variiert das Verfahren. So können die großen Flügel von modernen Langstreckenjets, z.B. des Airbus A350 XWB oder der Boeing 787 „Dreamliner“ über das ATL-Verfahren gefertigt werden. Die Automatisierbarkeit dieser Verfahren garantiert dabei eine stets gleichbleibende Produktqualität, die für diese strukturtragenden Bauteile unabdingbar ist. Allen Verfahren liegt jedoch das gleiche Prinzip zugrunde: Für das Erreichen der gewünschten Bauteildicke werden mehrere Einzellagen zu einem Laminat verbunden. Hierbei ist eine Lage ca. 125 µm dick, womit für eine Bauteilstärke von einem Millimeter acht Lagen benötigt werden. Beim Lagenaufbau werden die Faserschichten unterschiedlich ausgerichtet drapiert, wodurch sich ein sogenanntes „quasi-isotropes“ Materialverhalten ergibt. Anschließend kommen die gelegten Bauteile in den „Autoklav“, einen gigantisch großen Schnellkochtopf. Hierbei werden die Lagen unter hohem Druck bei Temperaturen von z.B. 180 °C verpresst und gleichzeitig wird das Harz, welches vorher in einem niedermolekularen Zustand unvernetzt vorlag, gehärtet.
Trotz der teilweise aufwändigen Herstellungsverfahren wird die Nachfrage nach CFK-Bauteilen aufgrund der vielfältigen Einsatzmöglichkeiten weiter zunehmen. Hierbei spielen auch Thermoplaste als Matrixmaterial eine große Rolle. In der Vergangenheit wurden viele Anwendungsgebiete, angefangen bei Leichtbaukonstruktionen für batteriebetriebene Fahrzeuge bis hin zu faserverstärkten Linienflugzeugen durch Weiterentwicklungen erschlossen. Dies wird auch in Zukunft durch neue Marktanforderungen und innovative Materialentwicklungen fortgeführt werden. Verbesserte Fertigungstechnologien bieten das Potential die Luftfahrt, die Automobilindustrie, sowie das Transportwesen insgesamt öko-effizienter und nachhaltiger zu gestalten.
Autoren: Fabian Hübner, Florian Schönl und Prof. Dr.-Ing. Volker Altstädt (Universität Bayreuth, Lehrstuhl für Polymere Werkstoffe)
Redaktionelle Bearbeitung: Lisa Süssmuth, GDCh
Literatur
[1] AVK Jahresbericht 2019 – Kurzfassung, Carbon Composites e.V.
Kommentare
Keine Kommentare gefunden!