3D-Druck von Polymeren im körpernahen Umfeld (3D-Druck Teil 2)
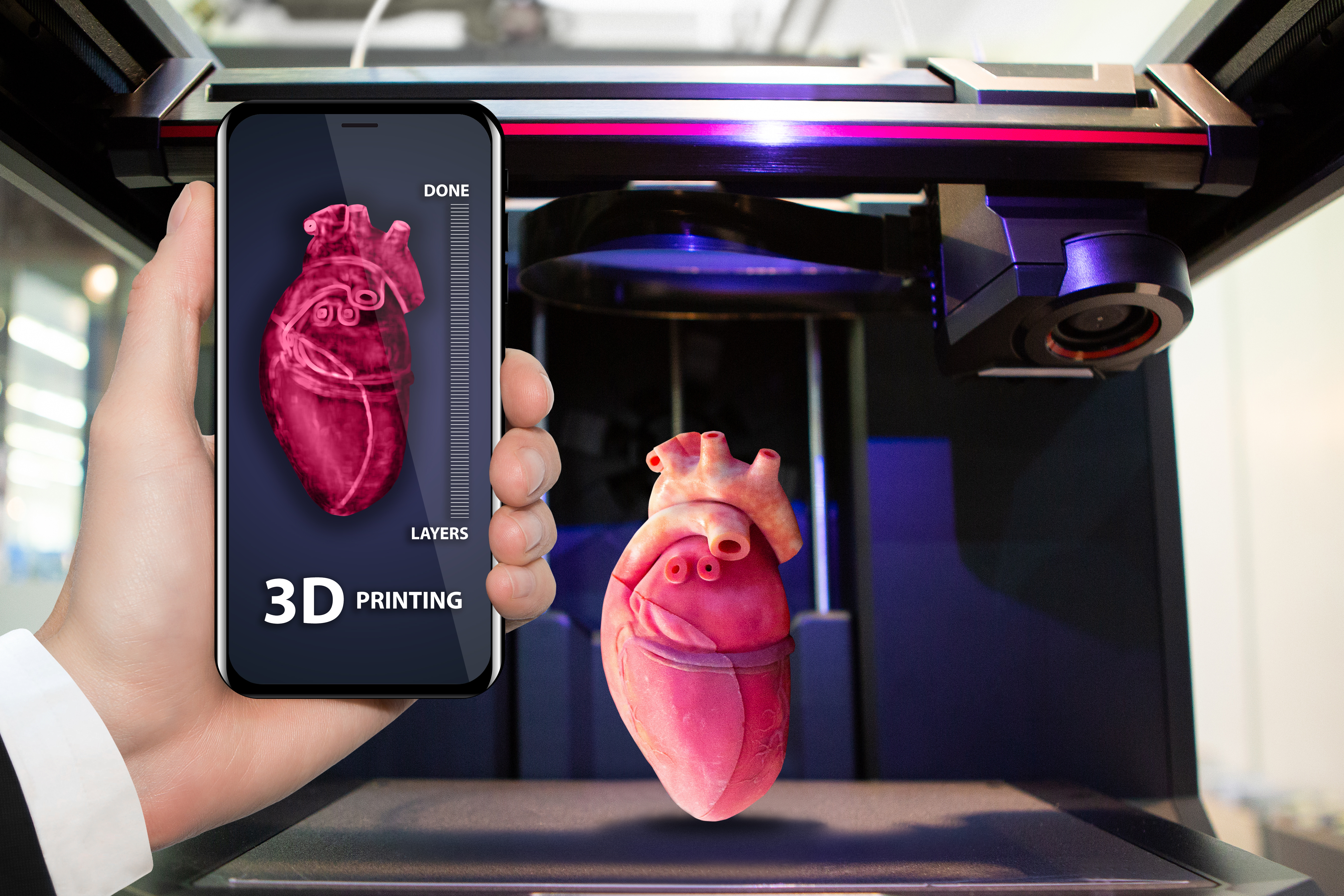
Von den im 3D-Druck eingesetzten Werkstoffklassen (Metalle1, Keramiken2, Polymere), bilden die Polymere die mit Abstand wichtigste Klasse, wenn es um typische Anwendungen im körpernahen Umfeld geht.
Sehen: 3D-Druck von Linsen
Brillen sind die immer noch die am weitesten verbreitete Sehkorrekturhilfe. Für den 3D-Druck von Linsen werden hauptsächlich modifizierte Inkjet-Drucker nach dem MMJ-Verfahren eingesetzt. Diese drucken auch komplexe Linsen-Geometrien auf Basis sehr niedrigviskoser polymerisationsfähiger Tinten. Als Tintenbestandteile werden dabei bevorzugt optisch hochbrechende Acrylat-Monomere eingesetzt, die während des Druckens Schicht für Schicht appliziert und mittels ultravioletten Lichts zur Polymerisation gebracht werden3. Der Einsatz von 3D-Druck-Verfahren zur Herstellung von Linsen macht immer dann Sinn, wenn entweder die Form der Linse oder die Funktion der Linse nicht über klassische Verfahren schnell und kostengünstig abgebildet werden kann. Analog zur Herstellung klassischer Linsenkörper müssen aber auch die 3D-gedruckten Produkte vor Einsatz in einer Brille in verschiedenen nachgeschalteten Schritten veredelt werden, zum Beispiel durch eine Reihe von Schutz- und Funktionsbeschichtungen.
3D-Druck von Brillengestellen
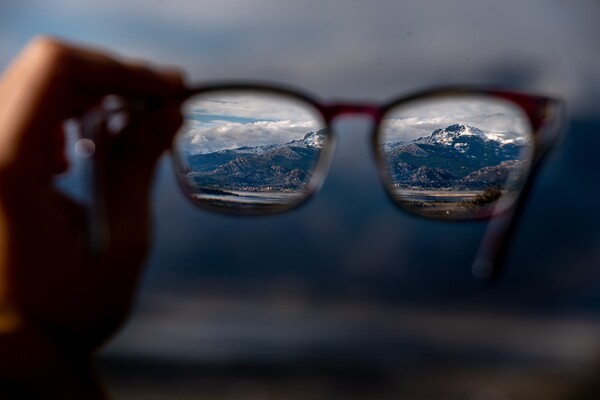
3D-Druck von Sehhilfen
© jom – stock.adobe.com
Eine zweite verbreitete Anwendung ist der Druck von Brillengestellen. Hier ermöglicht der 3D-Druck die Produktion individueller Passformen und Designs. Das aktuell bevorzugte Verfahren zur Herstellung von Brillenrahmen ist ein Pulversinterverfahren auf Basis von Polyamid-, Polyester- oder Polyurethanpulvern4. Die so erhaltenen leicht porösen Produkte werden im Anschluss an den Bauprozess häufig durch Infiltrationsverfahren nachbearbeitet, um sowohl die Eigenschaften wie auch die Optik (Oberfläche, Farbe) an die Kundenbedürfnisse anzupassen.
Nachbehandlungsverfahren im 3D-Druck
In der Regel erfordern die meisten 3D-gedruckten Produkte ein Nachbehandlungsverfahren zur Fertigstellung des Bauteils5. Dabei kann es sich um einfache Reinigungsverfahren, wie zum Beispiel die Entfernung von unreagierten Flüssigkeiten, Pulvern und Stützmaterial handeln. Nicht selten werden aber auch Verfahren zur Produkteveredlung wie Nachhärtung, Oberflächenglättung oder Einfärbung eingesetzt. Die Automatisierung dieser nachgeschalteten Prozesse ist eine notwendige Voraussetzung für den effizienten Einsatz des 3D-Drucks in industriellen Prozessen und damit ein hochrelevantes aktuelles Forschungsgebiet.
3D-Druck von Hörgeräten
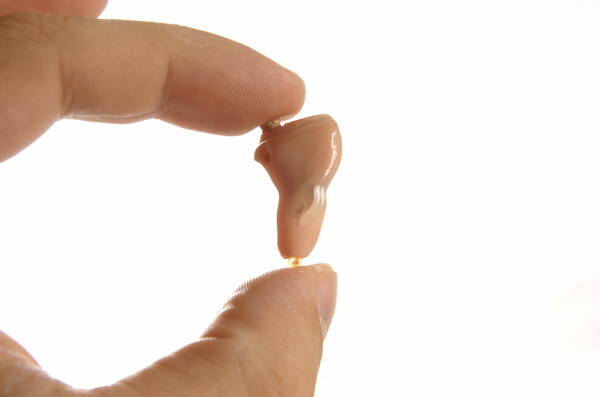
3D-Druck von Hörgeräten
© Dron – stock.adobe.com
Mittlerweile werden In-Ohr-Hörgeräte-Schalen und Ohrpassstücke fast ausschließlich mit 3D-Druckern hergestellt6. So kann die Passform der Schalen perfekt auf die unterschiedlichen Gehörgänge der einzelnen Träger abgestimmt werden. Zum Einsatz kommen hier 3D-Drucker, die nach dem SLA- oder DLP-Verfahren arbeiten.
3D-Druck von Prothesen
Die Zahl der veröffentlichten Anwendungen des 3D-Drucks zur Verbesserung der Beweglichkeit, Intaktheit und des Wohlbefindens von Patienten ist fast schon unüberschaubar. Prominente Beispiele sind äußere Prothesen7 von Gliedmaßen wie Arme, Beine, Hände und Füße. Prothesen können dabei funktional und anwendungsspezifisch sein, wie zum Beispiel Sportprothesen8. Eine weitere Anwendung ist der Druck von Epithesen9 als Ersatz oder Ausgleich von „Körperdefekten“ mit hauptsächlich ästhetischem Charakter. Innere Prothesen werden Implantate genannt. Sie befinden sich im Körperinneren und können dort nach Bedarf dauerhaft verbleiben, wie zum Beispiel künstliche Gelenke, Knie- oder Hüftprothesen10 und auch Herzklappenersatz11. Demgegenüber stehen offene Implantate, welche im Körperinneren befestigt werden, aber aus dem Körper herausragen, wie zum Beispiel Zahnimplantate12. Für die genannten Anwendungen kommen je nach Fragestellung heute verschiedene 3D-Druck-Verfahren und eine Vielzahl von Druckmaterialien zum Einsatz. Im Inneren des Körpers sind das häufig Metalle oder Keramiken, außerhalb des Körpers zumeist wieder Polymere.
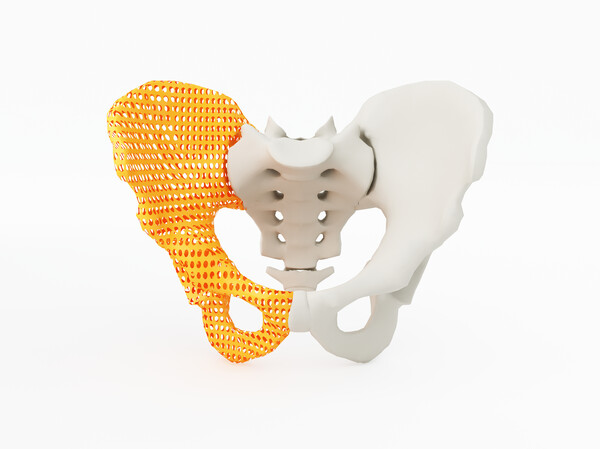
3D-Druck von Implantaten
© belekekin – stock.adobe.com
3D-Druck von orthopädischen Hilfsmitteln
Neben den Prothesen und Implantaten sind auch andere orthopädische Anwendungen wichtige neue Einsatzgebiete für den 3D-Druck. Orthesen13 dienen der Stabilisierung, Entlastung, Ruhigstellung, Führung oder Korrektur von Gliedmaßen oder des Rumpfes. Wie diese benötigen auch Schuheinlagen14 sowie Stütz- und Sitz-Einlagen15 einen hohen Individualisierungsgrad in der Fertigung und profitieren so von den Möglichkeiten des 3D-Drucks.
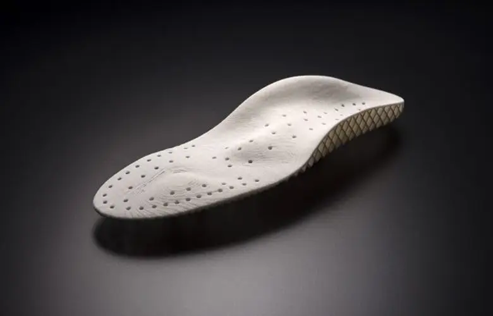
3D-Druck von orthopädischen Einlagen
© Covestro
Der 3D-Druck von Polymeren, die in ihrer Erscheinungsform sowohl weich und elastisch wie auch hart und zäh sein können, deckt fast alle Materialbedürfnisse gängiger orthopädischer Hilfsmittel ab. Kombiniert man die Fähigkeit von 3D-Druckern zur Herstellung geometrisch komplexer, funktionaler Bauteile mit modernen Scannern und KI-gestützter Auswerte- und Simulationssoftware, dann entstehen neue hocheffiziente Produktionsprozesse für orthopädische Hilfsmittel. Diese Entwicklung wird in absehbarer Zeit die Verfügbarkeit und Kostenstruktur von orthopädischen Hilfsmitteln zum Wohle aller Patienten revolutionieren.16
3D-Druck von Zahnkorrekturschienen
Im Grenzbereich zwischen medizinischer und ästhetischer Behandlung ist die Zahnkorrektur, mittels sogenannter Aligner Technologie17, angesiedelt. Das ist aktuell die größte bekannte Anwendung des 3D-Drucks, mit immer noch zweistelligen Wachstumsraten. Bei dieser Behandlung wird in einem ersten Schritt der Mundraum eines Patienten gescannt. Die Ist-Positionen von Zähnen sowie Unter- und Oberkiefer werden abgebildet, Fehlstellungen werden erfasst und aus der Ist-Situation ein Behandlungsplan in Stufen bis zum Erreichen einer Soll-Situation errechnet. Jede einzelne Stufe beschreibt eine leicht veränderte Zahn- und Kieferstellung, die im 3D-Druck realisiert wird und als Tiefzieh-Vorlage für eine Polymerfolie dient. Die 3D-verformte Folie wird im Anschluss zugeschnitten und weiter veredelt. Das Ergebnis ist jeweils eine Serie transparenter, fast unsichtbarer Zahnschienen (Aligner), die über einen Behandlungszeitraum von sechs bis achtzehn Monaten die Fehlstellung von Zähnen und Kiefern durch gezielte Druckausübung korrigieren. Das Material für den 3D-Druck der Vorlage ist wiederum eine reaktive Flüssigkeit, welche in einem SLA- oder DLP-Verfahren mittels ultravioletten Lichts schichtweise polymerisiert wird. Bei der Herstellung von mechanisch weniger anspruchsvollen Halteschienen (Retainern) und Knirschschienen wird das zweistufige Herstellverfahren häufig durch ein einstufiges Druckverfahren ersetzt und die Zahnschienen werden direkt im DLP- oder SLA-Verfahren gefertigt.
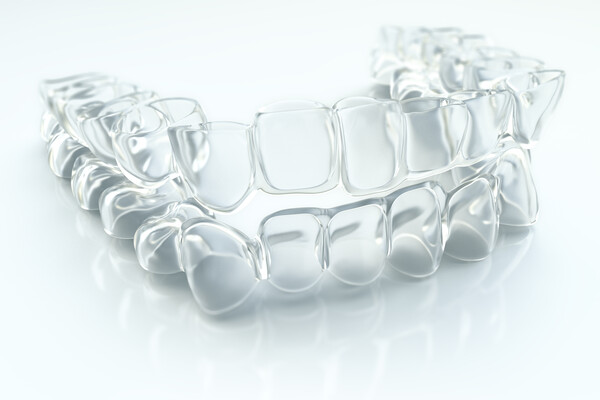
3D-Druck von Zahnkorrekturschienen
© crevis – stock.adobe.com
3D-Druck von persönlicher Schutz- und Hilfsausrüstung
Neben den eher „offensichtlichen“ Anwendungen im Dental- und Schönheitsbereich gibt es eine Reihe von 3D-Druck-Anwendungen, die auf eine Verbesserung unserer Sicherheit und Leistungsfähigkeit abzielen. Beispiele sind personalisierte, optimierte Schutzausrüstungen wie „maßgeschneiderte“ Helme und Protektoren im Sport und Arbeitsbereich. Als Schutzausrüstung der Zukunft sind sie bequemer, leichter und funktionaler als gängige Konfektionsware. Weiter arbeitet man an personalisierten Hilfsmitteln, die einer Vergrößerung oder dem Erhalt unserer Kräfte oder der Mobilität dienen. Warum sollten wir nicht auch im hohen Alter mit den Enkeln, im auf den eigenen Körper angepassten, gedruckten-Exoskelett18 in der „Ronaldo-Einstellung“ Fußball spielen?
3D-Druck von Organen
In großen Teilen noch Zukunftsmusik, aber schon jetzt Gegenstand intensiver Forschung ist der Ersatz von Körperteilen und Organen durch 3D-gedruckte, funktionale Repliken. Das Verfahren heißt im Allgemeinen Bioprinting19 und in einer speziellen Ausführung Bioplotting. Beim Bioprinting können neben Zellen, die man als wässrige selbstorganisierte Ansammlung von Biopolymeren beschreiben kann, auch unterstützende polymere Gerüststrukturen aus ausgesuchten künstlichen Polymeren, natürlichen Polymeren und bioresorbierbaren Polymeren verarbeitet werden. Stark vereinfacht dargestellt ist das Ziel dieser Technologie, durch eine Kombination von geometrischen Stützstrukturen, Selbstorganisation von Polymeren, Zellteilung und Zellspezialisierung innere Organe, wie das Herz20, sowie äußere Organe, wie zum Beispiel die Haut21, ersetzbar zu machen.
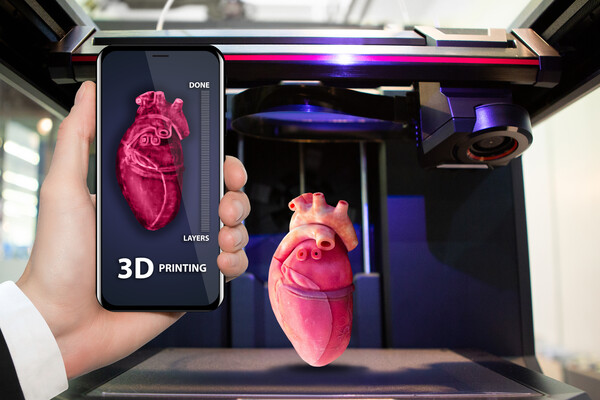
3D gedrucktes Herz
© scharfsinn86 – stock.adobe.com
3D-Druck von Medikamenten
Ein weiterer Forschungsschwerpunkt ist die pharmazeutisch-medizinische Anwendung des 3D-Drucks zur Herstellung von polymeren Wirkstoffträgern22. Hierbei besteht die Aufgabe des 3D-Drucks vor allem in der Formgebung. Diese kann kombiniert werden mit dem gezielten Design der Polymereigenschaften. Über die Polymereigenschaften wird zum Beispiel die Wasserquellbarkeit und die gezielte Abbaubarkeit in verschiedenen Organen des Körpers wie Mund, Magen, Darm oder Uterus beeinflusst. Der 3D-Druck generiert neben der äußeren Geometrie auch die innere Struktur des Wirkstoffträgers, zum Beispiel durch das Drucken gezielter Porenstrukturen, Transportkanäle und Verkapselungen. Ziel ist es, den Ort und die Geschwindigkeit der Wirkstofffreisetzung genau zu kontrollieren und das alles wie beim 3D-Druck üblich: Am liebsten lokal produziert, individuell abgestimmt und auf Zuruf!
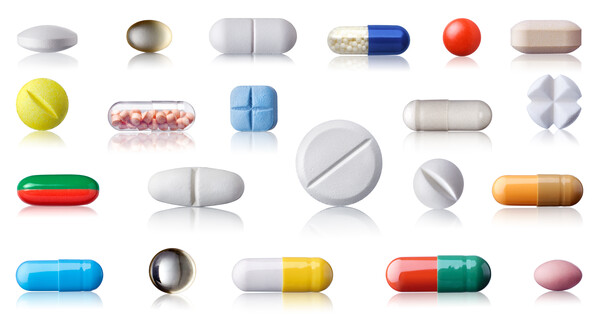
3D gedruckte Medikamente
© janvier – stock.adobe.com
Autoren:
Dr. Dirk Achten, R&D Digital Printing im Geschäftsbereich CAS bei der Covestro Deutschland AG;
Anne Hansen, PhD Student im Bereich Additive Manufacturing bei der Covestro Deutschland AG
Redaktionelle Bearbeitung: Maren Mielck, GDCh
Literatur:
https://3druck.com/medizin/3d-druck-in-der-medizin-teil-1-prothesen-2857877/ (aufgerufen 23.1.2021)
https://www.3dnetzwerk.com/mit-3d-druck-prothese-bei-den-paralympics-in-rio/ (aufgerufen 23.1.2021)
Jose, R. R., Rodriguez, M. J., Dixon, T. A., Omenetto, F., & Kaplan, D. L. (2016). Evolution of Bioinks and Additive Manufacturing Technologies for 3D Bioprinting. ACS Biomaterials Science and Engineering, 2(10), 1662–1678. https://doi.org/10.1021/acsbi
Kommentare
Keine Kommentare gefunden!