Wie verarbeitet man Polymere kontinuierlich? (Teil I)
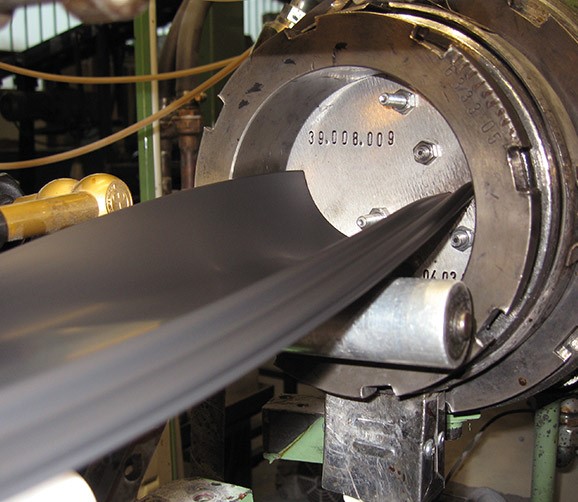
100 Jahre Makromolekulare Chemie
Polymere bilden die Basis für Werkstoffe aus sehr großen Molekülen. Diese Werkstoffe werden mit vielen unterschiedlichen Verfahren verarbeitet. Beispiele für Formgebungsprozesse sind Zerspanen, Gießen und Deformieren. Polymere lassen sich im Grunde in drei Kategorien einteilen: Thermoplaste, Elastomere und Duroplaste. Letztere werden erst nach der Formgebung zu einem Polymer geformt. Dies geschieht mittels einer chemischen Vernetzungsreaktion. In diesem Beitrag wird dies außer Acht gelassen. Thermoplaste und Elastomere müssen zuerst fließfähig gemacht werden, um sie zu formen, denn polymere Werkstoffe sind meist fest bei der Temperatur, bei der sie verwendet werden (meist Raumtemperatur). Es gibt zwei Methoden, um diese Fließfähigkeit zu erreichen: Die Erhöhung der Temperatur und das Auflösen in einem Lösungsmittel. Nachdem die Polymere fließfähig sind, können sie in die gewünschte Form gebracht werden. Danach muss das Material aushärten, so dass das Produkt formstabil wird und für seine Anwendung eingesetzt werden kann. Dazu nutzt man zwei Verfahren: Abkühlen (bei Thermoplasten) oder Vernetzen (bei Elastomeren). Und natürlich sollen etwaige Lösemitteln zuerst verdampft sein, falls das Polymer mittels Auflösen fließfähig gemacht wurde.
Polymere lassen sich mit drei verschiedenen Methoden kontinuierlich verarbeiten:
- Streichen
- Kalandrieren
- Extrudieren
Streichen
Zum Streichen muss das jeweilige Polymer in einem Lösemittel aufgelöst werden (vgl. Abb.1). Das gelöste Polymer wird auf einem Trägermaterial mittels einer Rakel gestrichen und anschließend in einen Ofen gegeben, wo es erhärtet. Das Lösemittel verdunstet und das Polymer verbindet sich mit dem Trägermaterial. Oft nutzt man dieses Verfahren, um Gewebe luft- oder wasserdicht oder widerstandsfähig gegen Schmutz zu machen.
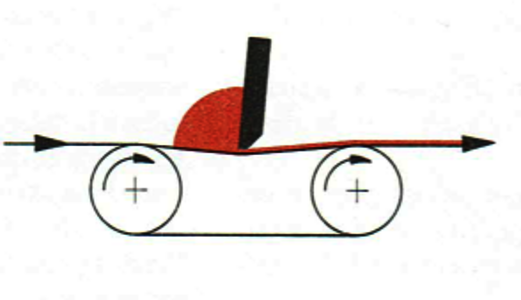
Abb. 1: Prinzip des Polymerstreichens
(Quelle: Schwarz / Ebeling / Lübke: Kunststoffverarbeitung; 6. überarb. Aufl. – Würzburg: Vogel 1991 ISBN 3-8023-0836-0)
Kalandrieren
Kalandrieren heißt der Formgebungsprozess, bei dem der Werkstoff zwischen zwei (oder mehr) Walzen zu einer dünnen und breiten Platte oder einem Fell ausgewalzt wird (vgl. Abb. 2). Platten und Folien aus Kunststoff (Thermoplaste) sowie Gummi (Elastomere) werden kalandriert. Das Kalandrieren nutzt man auch als Verfahren, um Gewebe mit Kautschuk zu belegen. Diese Halbfabrikate werden bei der Herstellung eines Reifens benötigt. Eine Folienanlage ist in Abb. 3 zu sehen.
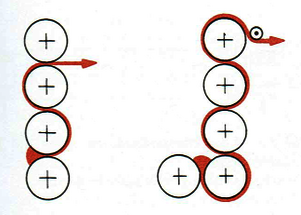
Abb. 2: Prinzip des Kalandrierens
(Quelle: Schwarz / Ebeling / Lübke: Kunststoffverarbeitung; 6. überarb. Aufl. – Würzburg: Vogel 1991 ISBN 3-8023-0836-0)
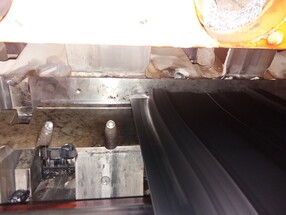
Abb. 3: Detailaufnahme eines Laufstreifens für einen LKW-Reifen
(Quelle: eigene Darstellung)
Extrudieren
Das kontinuierliche Formgeben eines Werkstoffes, der durch ein Mundstück gepresst wird, nennt man Extrudieren. Dabei nimmt der Werkstoff eine Form an, die der Öffnung in dem Mundstück, oft eine Leiste, ähnelt. Der Strang, der durch die Leistenöffnung gepresst wird, kühlt nach dem Verlassen der Leistenöffnung anschließend ab bzw. wird chemisch vernetzt. So wird der Strang formstabil und anwendbar für Gebrauch (vgl. Abb. 4).
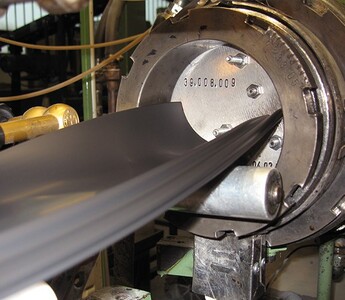
Abb. 4: Prinzip des Extrudierens
(Quelle: KraussMaffei)
Kautschuk verarbeiten: Ähnlich wie kalte Butter
Ein kurzer Exkurs: Um die Temperatur von Wasser zu erhöhen, reicht ein Topf auf einem Herd aus. Das Wasser, das nah an der Heizquelle ist, wird schnell warm, aber aufgrund der Schwerkraft und der niedrigen Viskosität (Größe für die „Zähfließendheit“) des Wassers steigt warmes Wasser im Topf nach oben und vermischt sich mit dem kälteren Wasser. Wenn man eine gebundene Suppe versucht aufzuheizen, muss man rühren, um zu vermeiden, dass die untere Schicht am Boden des Topfs verbrennt. Die Viskosität der Suppe ist bereits so hoch, dass die Schwerkraft die Suppe nicht mehr in Bewegung setzen kann.
Butter aus dem Kühlschrank kann man kneten, um sie fließfähig zu bekommen. Die Energie, die man beim Kneten in die Butter einbringt, führt zu einem leichten Temperaturanstieg. Dieser reicht aus um die Viskosität der Butter so weit zu reduzieren, dass man sie mit dem Messer auf der Brotscheibe verteilen kann. Beim Kneten zerbricht eine schwache Struktur in der Butter. Diese Struktur wird von Fettpartikeln ganz langsam zurückgeformt, sobald die Butter in Ruhe gelassen wird. Schmilzt man Butter in der Pfanne, entsteht eine niedrigviskose Flüssigkeit, auf der die Butter beim Erhitzen treibt, bis sie komplett aufgeschmolzen ist.
Ähnlich wie diese Beispiele ist es auch beim Aufbereiten von Kunststoffschmelzen und Kautschukmischungen. Die Viskosität der Schmelze ist jedoch so hoch, dass man sie ständig scheren muss, um eine gleichmäßige Temperatur in dem Werkstoff zu gewährleisten. Thermoplastschmelzen haben eine Viskosität in der Größenordnung von 10 bis 500 Pa × s. Kautschukmischungen sogar noch höher. Zum Vergleich: Wasser hat bei Raumtemperatur eine Viskosität von etwa 1 mPa × s und Olivenöl von 100 mPa × s. Je höher die Werkstofftemperatur, desto niedriger ist die Viskosität. Außerdem ist die Arbeit, die auf das Material ausgeübt wird, so hoch, dass schon dadurch die Temperatur des Materials ansteigt. Überschreitet die Viskosität eine bestimmte Schwelle, werden keine externen Hitzequellen mehr benötigt. In diesem Fall muss eher Energie aus der Schmelze durch Kühlen entfernt werden, um den Temperaturanstieg in der Schmelze in Grenzen zu halten.
Um die Schmelze oder Kautschukmischung durch ein Mundstück zu pressen, ist ein hoher Druck notwendig. Drücke von 20 MPa (200 Bar) sind nicht unüblich in der Verarbeitung.
Autor: Dr. Gerard Nijman (KraussMaffei Extrusion GmbH)
Redaktionelle Bearbeitung: Lisa Süssmuth/Maren Mielck, GDCh
Kommentare
Keine Kommentare gefunden!